Introducing OneTrack activity type and customer tracking
- OneTrack Marketing
- Jul 24, 2023
- 4 min read
Updated: May 6, 2024
Enhance warehouse performance with activity tracking and customer time management
Life in a warehouse moves fast.
Controlled chaos of product-in-product-out, where every minute is critical. How many of those critical minutes are unaccounted for in your operations?
Warehouse productivity has never been more important — or more difficult. Traditional labor management systems only take you so far in understanding your operations. And despite all of the tools and technology at your disposal, there are a several key questions that you can’t get an answer to:
Are operators routinely taking long lunches or breaks?
How long did that mixed freight truck take to unload?
How long do specific customer tasks or indirect processes actually take?
Answering these questions could save you millions each year through productivity and process improvements.
And that’s exactly why we’re launching our activity type and customer tracking — new features that give you visibility into all of your warehouse processes, so you can make key decisions and improvements.
Want a step-by-step playbook to eliminate idle time, skyrocket productivity, and optimize labor costs in your warehouses? Check it out here.
Track operator productivity with QR code sign-on
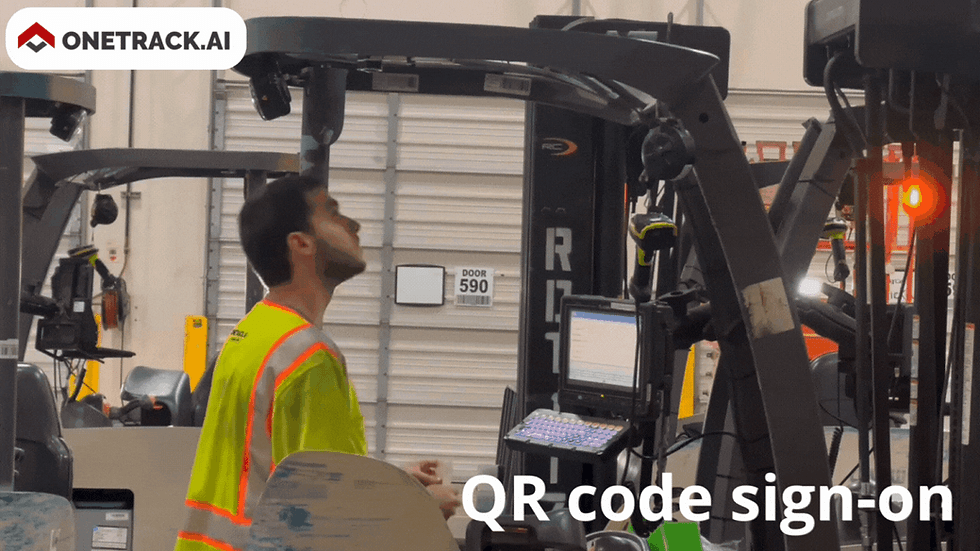
One of the quickest ways to make a substantial improvement to your warehouse productivity is to tighten up operators' routine activities such as delays at the beginning or end of shifts or taking long lunches or breaks.
As an example let’s say you have a 30-minute lunch policy in place, run two shifts, and 20 operators per shift.
If those operators took an extra 5-minutes per day over what the policy is, over the course of a month, that’s over 100 hours of lost productivity. And that’s just one warehouse and one activity.
But with QR code sign-on, operators simply scan into a lift and select an activity code. Upon sign on, they are automatically placed into the “work” code. “Break” and “Lunch” both come as standard options and other activities can be configured based on the operational needs. When they’re ready to take lunch they log into that activity code, and when they return they log back into the “work” code.
Now you have access to operator level reporting:
Which operators have a pattern of long lunches or breaks?
How long is it in-between scanning into work and when there is productivity motion on the lift?
You can even set up alerts so supervisors get notified in real-time when an operator is over their allowed break.

Benchmark and optimize processes with activity type tracking
Tightening up around shift start/ends, lunches, and breaks can be a huge win, but there is so much more that can be done to make your warehouse more productive.
Another key area to focus on are the unique processes that are completed each day in the warehouse. There are two main things to do from here.
1. Benchmark how long activities are taking so you can plan labor demands accordingly.
For example, you know that a specific site deals with a lot of inbound mixed freight trucks. Unloading these trucks takes a long time and if multiple come in during a certain window it can cause a logistical nightmare.
But with activity tracking, that same simple system that operators can use for lunch and breaks can be configured to track something like mixed freight.
Now you can see how long it actually takes to unload mixed freight, by site, shift, or operator. This insight allows you to make informed decisions to avoid bottlenecks.
Do you need to allocate more resources to unloading mixed freight?
Do you need to adjust appointment times of when trucks arrive?
Are there process improvements that are needed near loading doors to make processing mixed freight easier?
2. Optimization. Now that you have a more detailed understanding about activities, you can begin to adjust processes according to the data.
When operators aren’t able to operate their lifts productivity is being lost.
Non-productive activities happen on a daily basis and now that you know how much time is being consumed by these activities your team can begin to make operational adjustments to help avoid and prevent these types of slow downs.
Let's take a look at one of the main culprits of this: lift maintenance.
With the same activity type tracking, you can set up work codes like “Battery change”. An operator can log into that activity code to indicate that the lift battery is being changed, therefore they aren’t driving.
This opens up some interesting reporting:

You can see exactly when and how much time is required for these non-productive activities (like battery changes). Armed with this data, you can make informed decisions about the labor requirements for specific activities, and make the proper adjustments to optimize labor and process based on factual data.
Get visibility into your customer specific activities
It is a constant struggle in the public 3PL world. Asking “how much time do I spend on specific customer activities?”.
In a public warehouse setting, customers might all have specific required processes or activities, and to ensure you provide an exceptional customer experience, these processes are built into your offering.
But how much are these customer specific activities costing you in efficiency and productivity?
Productivity usually comes from well defined processes and repetition — when operators have to jump in and out of customer specific processes, things tend to slow down and can cause bottlenecks in your operations.
But now, using the same QR code sign-in functionality, you can get full visibility into how much time your team spends working on a specific customer's activities.
With this customer specific information you can now assign labor differently to meet certain customer requirements. Having this data will empower you to be a forward thinking business partner as you enter into discussions with a customer, showing them areas that can help improve business operations within their distribution channels. Chances are they too aren’t aware of how much time is being lost on a specific process.

Upgrade your warehouse productivity
Time is money, and every minute lost to an inefficient process or non-productive task means a hit to the bottom-line.
Up to this point, the visibility of non-productive activities, customer specific processes, and operator gap time hasn’t existed. With OneTrack you can now track operator sign on activity, specific activities, and activities by customers.
These new capabilities provide much needed insight into your processes so you can make valuable productivity improvements.
Comments