WarehouseOS Buyer's Guide
Everything You Need to Know About a WarehouseOS
The Ultimate Guide to Transforming Your Paper-Based, Incident-Prone Warehouse Operation into a Future-Proof Facility with a Warehouse Operating System (WarehouseOS).
Chapter 1
From Chaos to Control: Getting Started with a WarehouseOS
If your warehouse operation still relies on a “frankenstack” of paper-based processes, mounds of spreadsheets, a web of siloed warehouse technology, and inaccessible data without visibility into the why behind the numbers.
​
Or if any of these sound familiar:
Then it’s time to shake up the status quo.
"With big warehouses full of product you can't be everywhere and you can't see everything. The visibility OneTrack provides is critical and the ROI is immediately there. It's up to you to engage and use the tool correctly and build a program around it, but the technology works and the visibility allows you to really unpack and improve all aspects of your business."
Blake Martin
Director of Engineering

Traditional warehouse technology solutions like forklift telemetry systems or warehouse camera systems often fall short of expectations, so it’s understandable that leaders are skeptical of going all-in on a WarehouseOS.
​
But imagine one system to manage your warehouse safety, labor productivity, shipment quality, MHE fleet utilization, and continuous improvement. Getting critical visibility and data into the hands of your leaders (without needing IT to get involved) to make decisions faster.
​
So instead of...
You can disrupt the status quo.
​
It’s not just about survival—it's about thriving in an industry that's at a breaking point.
The best way to accelerate your operations is through a WarehouseOS.
This Warehouse Operating System (WarehouseOS) Buyer’s Guide outlines everything you need to know about a WarehouseOS. From what it is to the core features to look for so you can determine if a WarehouseOS is the right warehouse technology solution for you.
What is a WarehouseOS?
Warehouses are no longer an "out-of-sight, out-of-mind" operation; they're the backbone of modern supply chains that every industry relies on.
And what do warehouse operations rely on? A perfect balance of people, processes, and technology.
A WarehouseOS is more than just a tool or flashy warehouse technology.
By combining AI camera sensors, real-time video alerts, and customizable (and predictive) analytics all in a single platform, it’s a critical–but often missing–componant for modern warehouse management.
There's this assumption that the Warehouse of the Future has to be fully autonomous. I don't think that's true. It's built on visibility. There is so much time lost on fundamental things that if you could see and fix, you would make much more reliable and cost effective improvements.
Marc Gyöngyösi
CEO
.png)
Complete warehouse visibility has to be step 1 for any operation looking to improve. Because you can’t solve problems that you can’t see.
​
From ensuring workplace safety and enhancing warehouse productivity, to maximizing MHE usage and maintaining the highest standards of shipment quality, a WarehouseOS provides a holistic view of warehouse operations offering:
And so much more.
​
A WarehouseOS is ultimately about providing critical visibility—bridging the gap between disconnected systems and processes, and making data truly actionable. It lays the foundation for warehouse excellence.
This empowers warehouse leadership to elevate their operations to the next level, either at a single site or across an entire warehouse network.
​
So, what does that look like in action? It starts with building a gold standard warehouse—one that sets the benchmark for safety, productivity, and quality.
Become the Gold Standard with a WarehouseOS
A "gold standard" warehouse is like a model home in a new neighborhood.
It's the ideal version—a benchmark for how every warehouse in a network should operate. As Justin Emmons, Director of Customer Operations at OneTrack, described on an episode of Warehouse Visionaries:
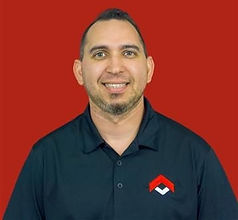.jpeg)
“Just like a model home showcases the ideal layout and features, a gold standard warehouse represents the optimal setup for operational excellence. It includes all the functionality, coaching policies, and processes necessary to operate effectively. This ‘model’ establishes a blueprint for other warehouses within a network, ensuring standardization across the board.”
Justin Emmons
Director of Customer Operations, OneTrack
Achieving the gold standard means you’re the epitome of safety, productivity, and quality.
​
This requires a relentless focus in three critical areas of your operations that a WarehouseOS can pull together all in a single platform–your people, processes, and product.
The visibility that a WarehouseOS offers has a massive impact on each area.
Gold Standard: How a WarehouseOS Benefits People
Your people are the foundation of a gold standard site.
​
A WarehouseOS can significantly reduce safety incidents, and improve worker safety and accountability. For example, with AI-powered video monitoring and automated video alerts, companies like ID Logistics have seen an 84% decrease in overall safety incidents and a 99% reduction in phone use violations.
And by using video like game film, supervisors can provide instant feedback based on video evidence, allowing for more proactive and value-added coaching that builds a culture of accountability.
​
​As Matt Ireland, Director of EHS at Holman Logistics, said:
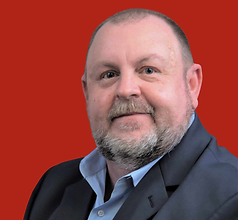
“Supervisors want to stick up for their team. But sometimes that means making excuses for them instead of coaching them. With video evidence, supervisors can’t make excuses for their team members. It helps them grow and be better leaders by holding people accountable.”
Matt Ireland
Director of EHS, Holman Logistics
Creating a safer and more accountable culture, where every worker has a voice and constructive collaboration is encouraged, leads to higher morale and lower turnover–addressing a key issue in warehouse labor.
Gold Standard: How a WarehouseOS Benefits Processes
If people are the foundation of your operation, then processes are the walls.
Turn your paper-based processes into a digital system that makes data more accessible and easier to uncover opportunities for process improvements.
A WarehouseOS can analyze all of your plant and employee performance data to uncover where you’re losing the most productivity–and why.
For example, companies like CJ Logistics have improved UPH by 11% thanks to complete visibility into its processes and how supervisors coach on performance, surfacing insights that they’ve never had before to help better manage labor productivity.
With network-wide visibility, companies can standardize operating procedures across multiple warehouse locations, ensuring consistency regardless of site or shift.
​
Now, instead of searching through hours of CCTV footage, managers can access video instantly–whether it’s a safety event, process breakdown, or something else entirely–to cut investigation times, coach according to your company’s policies, and focus on making strategic, value added process improvements.
Gold Standard: How a WarehouseOS Affects Product
As Ryan Donovan, President of States Logistics, recalled about his mentors when he first started in the industry over 35 years ago:
On an Insider Session on how to build world-class warehouse operations through innovation, Ryan also recounted earlier in his career printing out 4-inch thick bulk charts that had product SKU information and where its location was in the warehouse. He said:
​
“And you use this to go find product out in the warehouse and figure out what you were picking. And that was updated every few days. And at the end of the month, you updated the customer and you made sure that your inventory is matched and everything's right.”
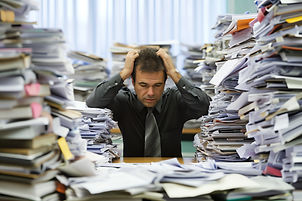
And while things have certainly come a long way since then, many operations still practice other outdated and manual process such as taking pictures of every load before it leaves the warehouse.
Manually capturing and organizing pictures is time-consuming and increases your labor costs. Plus, inconsistent or missed photos can lead to gaps in documenting your shipping processes, making it even harder to track accountability.
The saying may be true that a picture is worth a thousand words, but photos alone don’t provide the full context that you need. It lacks complete visibility.
A WarehouseOS can automate the load verification process, eliminating the hassle and headaches of manually taking and managing photos.
​
By automatically recording every shipment and ensuring product integrity, if there’s a damage claim, companies can instantly validate whether the product left in good condition, reducing unnecessary refunds or disputes.
For example, Carrie Ferrone, Senior IT Lead of Warehouse Systems for ID Logistics said:
The visibility that a WarehouseOS provides ensures proactive issue resolution, improving relationships with customers and reducing reputational risks by proving that their shipment quality is your top priority.
Visibility is not just about seeing—it’s about knowing, understanding, and making data-driven decisions to improve safety, productivity, and quality.
​
Unlike spreadsheets, traditional forklift telemetry systems, and basic warehouse camera systems, a WarehouseOS can bring real-time visibility to your entire operations–and bring your gold standard vision to life.
When investing in a WarehouseOS to achieve the gold standard, choose a system that can grow with your operational needs and adapts to your unique processes and workflows.
At the very least, you need these core features in your WarehouseOS.
Chapter 2
Core Features to Look for in a WarehouseOS
The ultimate goal of any warehouse is simple: get product out the door (safely). When forklifts are sitting idle, or moving around without pallets on them, you’re losing money.
At the end of the day, you're looking to be profitable.
Your warehouse manager wants faster load times, fewer delays, and better bottom-line results.
In the past, you’d have to create a spreadsheet to track barcode scans and timestamps, hoping it’ll somehow drive employees to be faster and more efficient.
​
But, often, instead of motivating them, it backfires spectacularly.
​
Warehouse performance management becomes a maze of KPIs tied to timestamps in spreadsheets, with no clear insight to the why behind those numbers.
Suddenly, employees, pressured to hit their goal at all costs, start cutting corners—compromising safety, increasing accidents (many of which go unreported), and risking product damage (and your reputation).
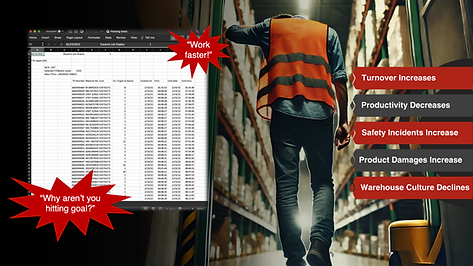
OneTrack's WarehouseOS changes all of that.
By getting complete visibility into operational blindspots, you can make critical improvements based on what's really happening on the floor (not on spreadsheets).
1. Complete Warehouse Visibility
You can’t solve problems that you can’t see.
​
So before you can actually start solving problems, you need to invest in visibility. OneTrack uses AI camera systems and sensors to provide real-time, comprehensive visibility into all aspects of warehouse operations.
Static systems, like traditional security cameras with limited fields of view, or rigid solutions that are only compatible with specific MHE providers, can’t keep up with the dynamic needs of modern warehouses.
A WarehouseOS like OneTrack offers a scalable solution by integrating AI-powered cameras and customizable analytics that adapt with your operations and provide complete visibility across your entire warehouse—putting you in the driver’s seat of your operations.
As your warehouse operation grows and changes, our flexible WarehouseOS ensures your visibility scales seamlessly alongside it.
2. AI-Powered Safety Monitoring
Keeping your team safe isn’t just about policies—it’s about putting people first and having real-time visibility into what’s actually happening in your warehouse so you can change behaviors and prevent incidents.
​
A WarehouseOS powered by AI helps you do just that.
Eyes in The Warehouse, 24/7.
AI watches for unsafe behaviors like phone use, reckless driving, or impacts and instantly alerts supervisors with video evidence.
Stay Ahead of Risks.
By analyzing trends, the system flags potential safety hazards before they become incidents.
Coach with Confidence.
Supervisors can use real-life (anonymized) footage to train employees, correct mistakes, and build a culture of accountability.
Prevent More Accidents.
Fewer incidents mean a safer, more productive team—and a workplace where safety isn’t just a policy, it’s the culture.
3. Productivity Optimization Tools
Running an efficient warehouse isn’t just about working harder or faster—it’s about working smarter.
​
A WarehouseOS takes the heavy lifting out of warehouse labor management.
Workflows That Run Themselves.
Automate complex tasks so leadership can focus on hitting KPIs, solving problems, and growing the operation.
Make the Most of Your Team.
Track idle time, identify bottlenecks, and ensure labor is being used where it’s needed most.
Real-Time Labor Standards.
Go beyond static benchmarks with AI-driven insights that adjust dynamically to meet your daily operational goals.
Right People, Right Place.
Match labor and equipment to demand so you’re never short-staffed during a rush—or overspending during a slow period.
4. Quality Control & Error Prevention
A single mistake in a warehouse can mean lost revenue, customer complaints, compliance headaches–or worse.
A WarehouseOS helps you stay ahead of issues before they escalate. Not only when it comes to people and processes, but also product quality.
Video-Verified Shipments.
Every load is automatically recorded, providing proof of quality and accuracy.
Catch Errors Before They Happen.
Track every item at every touchpoint to flag potential issues before they reach customers.
Build Customer Trust.
Show video proof of proper product handling to resolve disputes quickly and transparently.
Improve Every Day.
The system pinpoints recurring issues and suggests more efficient workflows so you can keep getting better, shipment after shipment.
5. Real-Time Data & Analytics
You shouldn’t need a team of engineers to make sense of your warehouse data. And that data should be accessible at your fingertips when you need it the most to make decisions.
​
A WarehouseOS makes data analysis easy and actionable:
Instant Alerts, Instant Action.
Get notified of key events the moment they happen so you can respond before small issues turn into big problems.
See the Future, Not Just the Past.
AI analyzes trends and real-time data to do more than highlight what happened and why—it tells you the smartest next step.
At-a-Glance Dashboards and AI Data Analysis.
See performance, safety, and quality metrics in real-time across your entire network for every site and employee. And have your own AI chat assistant that analyzes historical performance data, your company policies, and human-in-the-loop observations to create custom coaching plans.
6. Seamless Growth & System Integration
Your warehouse operations are always evolving. Your technology should keep up.
​
A WarehouseOS scales effortlessly and works with what you already have:
Plug Into What You Use.
Integrates smoothly with ERP, WMS, LMS, and TMS platforms for a connected, streamlined operation.
Works Everywhere.
Compatible with all equipment types and environments.
Expand Without the Headaches.
Scale across multiple sites with minimal disruption while keeping operations running smoothly.
Always One Step Ahead.
The system continuously learns and adapts, ensuring it grows with your business—not against it.
No IT Needed.
We get it, IT help is often hard to get. So you need a WarehouseOS that requires no IT resources, with AI cameras installed by (and the solution fully managed by) your WarehouseOS provider.
By combining these core features, a WarehouseOS can turn even the most struggling warehouse operation into a data-driven profit center that is safer, more productive, and higher quality.
​
Now that we’ve covered the must-have features of a WarehouseOS, the next step is seeing how it all comes together in the real world. Features are only valuable if they translate into meaningful improvements—reducing safety incidents, optimizing productivity, and ensuring shipment quality.
So, let’s explore how a WarehouseOS works in action, solving the biggest challenges warehouses face every day.
Chapter 3
How a WarehouseOS Transforms Daily Warehouse Operations
Warehousing plays a crucial role in the supply chain, but it’s also full of challenges that can disrupt operations, increase costs, and compromise safety.
Unlike a traditional Warehouse Management System (WMS) that mainly tracks inventory and orders, a WarehouseOS is the command center for your entire operation. So you can solve your biggest challenges head on and improve workplace safety, labor productivity, and shipment quality.
By integrating data, automation, and AI-driven decision-making into a single platform, a WarehouseOS gives you real-time visibility into every aspect of your warehouse. Let’s explore some of the most valuable ways it can be put to work.
1. Visibility into People: Safety, Accountability, and Productivity
Use Case
Scenario
Solution
Targeted Employee Coaching to Improve Safety
A forklift operator has recurring incidents or frequent near misses.
The WarehouseOS flags these trends and recommends specific coaching tailored to address the unsafe behavior. Supervisors receive actionable insights, enabling targeted training to correct the issues and foster a safer workplace.
Using AI and Video for Labor Optimization
Productivity levels are falling due to excessive idle time.
The WarehouseOS integrates AI-analyzed video and performance data to identify inefficiencies. Managers can use the insights to take corrective actions, such as streamlining workflows or providing feedback, ensuring more effective labor use.
Real-Time Safety Alerts and Incident Prevention
An employee is using a phone while operating machinery.
The WarehouseOS sends instant alerts with video evidence to supervisors. This not only allows for immediate correction but also provides data to prevent similar incidents in the future.
2. Visibility into Processes: Running Your Operation like Clockwork
Use Case
Scenario
Solution
Proactive Exception Tracking for Safety, Productivity, and Quality
A forklift hits shelving and damages product.
The WarehouseOS uses machine learning to detect exceptions as they occur, flagging them for review. Supervisors receive detailed video and data to correct these issues and ensure they don't recur.
Continuous Improvement Through Workflow Optimization
Bottlenecks frequently slow down picking zones.
By analyzing historical data, the WarehouseOS suggests actionable changes such as reconfiguring layouts or redistributing inventory to streamline operations and prevent future delays.
Automating Routine Workflows
Time-consuming and inconsistent safety checks.
The WarehouseOS automates these tasks, reducing manual effort and ensuring compliance, while allowing your team to focus on higher-value work.
3. Visibility into Product: Quality, Accuracy, and Traceability
Use Case
Scenario
Solution
Item-Level Traceability with Video Evidence
A product is damaged in transit, and there’s no clear accountability.
The WarehouseOS tracks every item's handling history and provides video evidence, offering a complete picture of its movement through the warehouse and ensuring end-to-end traceability.
Automated Load Validation to Eliminate OS&D Issues
Customers frequently report damaged or incomplete shipments.
The WarehouseOS validates load integrity with high-resolution cameras and sensors, ensuring every shipment meets quality standards and preventing surprises at delivery.
Quality Control Through Proactive Alerts
Improperly secured loads repeatedly cause product damage.
The WarehouseOS identifies these patterns, sends alerts, and suggests procedural changes to prevent the issue from recurring.
4. Connecting the Dots Between People, Processes, and Product
Use Case
Scenario
Solution
Smarter Fleet Management
Forklift downtime disrupts operations and delays shipments.
The WarehouseOS tracks real-time equipment usage and recommends predictive maintenance schedules, minimizing downtime and extending equipment life.
Unified Exception Tracking Across Operations
Difficulty pinpointing the root cause of operational problems.
The WarehouseOS monitors exceptions holistically, providing insights and solutions to improve safety, productivity, and quality simultaneously.
Comprehensive Insights for Long-Term Improvement
Travel paths are unnecessarily long, reducing efficiency.
By integrating data from employees, workflows, and inventory movement, the WarehouseOS highlights opportunities to optimize layouts and reduce travel times, boosting overall productivity.
We want to make it as easy as possible to understand if OneTrack is right for you. Below you’ll find answers to some common questions that we get and a collection of resources you can use while evaluating OneTrack.
With a WarehouseOS, you get the visibility you need into every aspect of your warehouse—people, processes, and product. Whether it’s:
-
Tracking safety risks in real time
-
Optimizing workflows and labor productivity
-
Improving product traceability with video evidence
-
Automating routine tasks to reduce manual effort
-
Delivering actionable insights for continuous improvement
A WarehouseOS ensures your operation is always running at peak condition.
Chapter 4
How a WarehouseOS Stacks Up to Legacy Warehouse Technology
You want safer, faster warehouse operations, but other approaches just aren’t cutting it:
​
-
Spreadsheets with static data delay access to real-time information, and you can't see the why behind performance trends.
-
A forklift telemetry system doesn't capture nuanced driver behaviors or insights into broader warehouse operations.
-
A warehouse camera system only records footage without providing proactive alerts, operator POV, or insights to identify trends.
Warehouse operations are like an iceberg, where what you observe is just a fraction of what's actually happening beneath the surface—safety events and behaviors that go unseen and unreported.
Only with visibility into your operation can you identify the root cause (or leading indicator) of an event and take corrective action to fix it and prevent similar occurrences from happening again.
A WarehouseOS provides the visibility you need to have a critical eye and uncover the hidden hazards lurking below the surface of your operations to meaningfully improve safety, productivity, and quality.
Forklift Telemetry System vs. Warehouse Operating System
Two warehouse technologies that are often compared are traditional forklift telemetry systems and a WarehouseOS.
Both aim to make workplaces safer, but how they achieve this—and the results they deliver—are worlds apart.
Let’s dive into how they stack up.
Forklift Telemetry is a Reactive Tool
A forklift telemetry system is solely focused on forklift monitoring and relies on G-Force thresholds, which is designed to detect impacts or shocks experienced by forklifts based on how much it accelerated or decelerated.
When a forklift exceeds a certain threshold, the system sends an alert or locks out the forklift. It sounds straightforward, but G-Force forklift systems aren't enough for forklift safety. Here’s why:
The result?
​
A forklift abruptly shutting down leads to significant disruptions in warehouse operations.
Including safety risks for workers and potential damage to product, and also decreased productivity from work coming to a halt and the inconvenience of needing to restart the forklift every time it locks out.
"Our experience with telematics was over-promised and under-delivered. We hoped to improve efficiency, visibility, and safety by integrating it into new equipment. But, we faced several challenges and telematics didn't deliver on that promise."
Daniel Alvarado
Director of Operations

These systems also fall short when it comes to reporting or offering insights into the root causes of incidents. That’s a major gap. And that’s where a WarehouseOS shines–providing visibility into your blindspots.
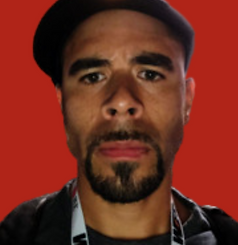
“As for reporting, the data we received with telematics didn’t provide the visibility we needed to take immediate action. We found ourselves chasing issues rather than proactively fixing them. With OneTrack, we finally got the visibility and functionality we were looking for. It was a significant upgrade over telematics, not just delivering on our expectations but exceeding them."
Daniel Alvarado
Director of Operations, Inland Star
A WarehouseOS is a Proactive Solution
A WarehouseOS takes a radically different approach than traditional forklift monitoring solutions.
AI cameras put you in the driver’s seat of your operation.
​
Unlike using unreliable G-Force thresholds that forklift telemetry systems rely on, a WarehouseOS uses computer vision to learn what’s normal in your warehouse and what’s not. This minimizes false positives that plague telemetry systems and ensures alerts focus on what really matters for you.
Plus, when an alert happens, you don’t get a vague notification or a locked out forklift without any context why it happened. Instead, you get video evidence so supervisors can see what happened, understand why it happened, and take corrective action, without disrupting the operation.
This visibility fosters accountability and empowers supervisors to have more value-add coaching conversations, contributing to a safer and more productive warehouse culture.

"For us, productivity is all about keeping people on task, consistent, and removing any roadblocks for our employees. OneTrack has brought complete visibility into our processes and how we coach on performance, bringing insights we’ve never had before to better manage our labor productivity."
Laura Adams
SVP of TES, CJ Logistics America
And unlike forklift telemetry, a WarehouseOS doesn’t wait for accidents—you can prevent incidents before they happen.
A WarehouseOS proactively identifies early warning signs of safety issues, like unsafe turns, phone use, or obstacles on the floor (which not only risk worker safety and product quality, but can also hinder productivity). With this visibility, supervisors can address the root causes of potential problems before they escalate.
With a WarehouseOS, the outcomes are clear:
-
Fewer incidents
-
Less downtime
-
Better accountability
-
More efficient operations
So when it comes down to choosing between a forklift telemetry system or a WarehouseOS, the choice is clear—a WarehouseOS.
We want to make it as easy as possible to understand if OneTrack is right for you. Below you’ll find answers to some common questions that we get and a collection of resources you can use while evaluating OneTrack.
Warehouse Camera System vs. WarehouseOS
If you’re still relying on traditional warehouse camera systems (CCTV) to monitor operations, you’re likely spending too much time rewinding footage instead of preventing issues in the first place.
​
While security cameras have been a staple in warehouses for decades, and should be used in most operations, they were never designed to proactively improve safety, productivity, or product quality.
Here’s why your warehouse CCTV isn’t enough (and what to do instead).
Legacy Warehouse Camera Systems
Security cameras have been around for a long time. They do their job—recording footage—but they come with two major downsides.
Limited Coverage and Blind Spots.
Traditional warehouse CCTV cameras are mounted in fixed locations. And since they’re static, they can only record the areas directly in their line of sight.
When a warehouse is hundreds of thousands of square feet, there are many critical activities happening beyond the range of a security camera, such as:
​
-
Between aisles where it's difficult to position cameras
-
Around blind corners where forklifts and workers are frequently moving
-
In high-traffic zones where a single camera angle is not enough to capture the full picture of what’s actually happening.
Reactive Instead of Proactive.
Legacy CCTV systems only provide post-incident documentation. That means:
An accident happens (which you hear about because a security camera doesn’t send you an alert in real-time). You spend hours reviewing footage (if it even caught the event) to figure out what went wrong.
And by the time you maybe figure out what happened, the damage has already been done and another incident has already happened somewhere else in the warehouse.
Warehouse Operating System
A WarehouseOS doesn’t just passively record footage—it actively detects and prevents safety, productivity, and quality issues before they escalate.
​
Unlike static CCTV cameras, a WarehouseOS uses AI-powered sensors strategically placed on forklifts and MHE, literally putting you in the driver’s seat of every piece of equipment in your fleet. Plus mounted in high-traffic zones and dock areas.
This ensures that every inch of your warehouse is covered—without blind spots.
And with real-time, video-based alerts, you no longer need to spend hours reviewing blurry CCTV footage (or worse, if the warehouse camera system never even recorded the event).
Instead, you receive instant (and automated) notifications for critical events like forklift impacts, near misses, product damage, and unsafe operator behavior. Which you can then proactively coach on to prevent incidents from escalating or happening again.
How?
By detecting early warning signs of unsafe behaviors such as distracted driving, not looking in the direction of travel, and other leading indicators that supervisors can then coach on using video like gamefilm to hold operators accountable and correct behaviors before they lead to an accident.
And with predictive analytics, you’re not just reacting to problems—you’re actively stopping them before they occur.
A CCTV system simply does not have the capabilities to provide this level of operational insights.
​
On the other hand, a WarehouseOS goes beyond surveillance (and just safety) by offering customizable reporting to analyze productivity trends, lift utilization metrics to maximize your forklift fleet, and workflow analysis to identify process bottlenecks.
With real-time data, you can make informed decisions to improve every facet of your operation—people, process, and product.
The bottom line: Legacy warehouse camera systems might have been enough in the past, but today you need a system
that does more than just watch.
If you’re ready to move beyond passive surveillance and stop relying on outdated warehouse camera systems, then it's time to invest in a WarehouseOS.
​
In the next section, we provide a checklist for selecting the right WarehouseOS (and why).
Chapter 5
The Ultimate Checklist for Investing in a WarehouseOS
It’s no longer a question—instead of relying on 8 systems, like forklift telemetry or outdated warehouse cameras, that your team has to learn, paper processes, and spreadsheets, there’s a better way to operate your warehouse.
​
You can finally get the complete visibility into your entire operation that you’ve been missing, all in one Warehouse Operating Systems.
And the results speak for themselves.
So to help you navigate your decision to invest in a WarehouseOS, we’ve put together a checklist of must-have WarehouseOS features.
Essential WarehouseOS Features You Must Have
1. Real-Time Exception Tracking​​
Keep safety violations in check with AI-powered monitoring that reduces costly incidents and keeps operators accountable. AI Cameras Analyze Every Movement. Mounted on forklifts, dock doors, and overhead structures, these cameras continuously record and analyze activity. Instant Detection of Unsafe Behavior. Whether it’s phone use, PPE violations, reckless driving, or something else entirely that goes against your warehouse policies, AI flags it in real-time. Automated Supervisor Notifications. Get real-time alerts with video proof so you can respond immediately. And so your inbox isn’t flooded with notification, it prioritizes events based on what’s most important to you and your warehouse operations. Risk Scorecards & Trend Analysis. Spot patterns, and identify high-risk operators and most-help needed workers to proactively prevent future incidents and create tailored coaching plans. With OneTrack’s WarehouseOS, you can address issues before they escalate, proactively prevent incidents, ensure consistent coaching across your site locations, and reduce equipment and product damage.
2. Forklift Fleet Monitoring
Maximize forklift utilization, prevent equipment and rack damage, and reduce costs with AI-driven forklift fleet management. 24/7 Fleet Tracking: Monitor the movement of every forklift including idle time. AI identifies underused forklifts and overworked assets. Impact Detection with AI Sensors: AI differentiates between normal warehouse operations and actual safety incidents. Predictive Maintenance Alerts. Avoid equipment breakdowns with smart AI alerts that detect wear and tear to predict failure. And reduces downtime by triggering proactive maintenance requests. Heat Mapping and Route Optimization. AI analyzes travel paths to find inefficiencies and recommends changes for smoother, safer operations. With a WarehouseOS capable of comprehensive forklift fleet management, you can reduce maintenance costs, extend equipment life, right-size your fleet (no more underutilized or overworked equipment), and pinpoint high-risk operators for targeted coaching.
3. Video-Based Labor Management​​
Eliminate wasted time, boost productivity, and keep workers accountable with video-based labor management. 1. AI Productivity Tracking. Analyze picking, staging, loading, and unloading in real-time with video alerts and predictive recommendations to improve productivity. 2. Bottleneck Detection. AI flags areas where workers are taking longer than expected and suggests recommended next steps to alleviate slowdown and create a more productive environment. 3. Automated Coaching Alerts. If an employee falls short of productivity benchmarks, AI sends a real-time coaching alert with video insights. 4. Dynamic AI Labor Standards. AI creates site-level and employee-level performance benchmarks tailored to each warehouse. And adjusts for seasonal demand and operational needs. With a WarehouseOS that offers video-based labor management, you can pinpoint and correct inefficient processes, standardize performance metrics across sites, and improve worker accountability by having data-back and consistent coaching conversations using video instead of hunches.
4. Item-Level Track & Trace
Put your shipment quality on autopilot down to the last detail to ensure product leaves your warehouse in top condition, every time. 1. Automated Load Recording System. With AI sensors mounted on dock doors and forward facing on your loading equipment, you can automatically record every load for complete visibility into potential issues to maintain product quality at every step. 2. Instant OS&D Dispute Resolution. Prove to customers and end locations that product quality is at the top of your priority list. Easily bring video proof to resolve OS&D claims and validate (and continuously improve) your shipment quality. 3. Proactive Damage and Shortage Detection. AI sensors scan throughout the loading process to identify potential damages and can even read LPN or barcode information to ensure the right product goes on the right truck, damage-free. 4. End-to-End Quality Assurance Monitoring. Get visual evidence every time product is touched, from the moment it enters your warehouses, to the moment it's shipped back out. And all stored in a searchable database by location, LPN, order number, or operator. 5. Advanced Warehouse Temperature Monitoring. Get notified every time warehouse conditions fall out of optimal range with OneTrack's temperature and humidity monitoring to keep product (and your bottomline) in peak condition. With a WarehouseOS providing item-level track and trace, you can put an end to costly and time-consuming OS&D claims, show your customers proof of how carefully product is being handled, and automate load validation and tracking to ensure product leaves your warehouse in perfect condition, every time.
5. Guided Coaching
Turn data and video into actionable and consistent coaching opportunities that actually improve operator performance. 1. AI-Powered Video Insights. AI cameras installed on forklifts and throughout the warehouse detect unsafe behaviors and productivity gaps. When an incident occurs (e.g., an impact, phone use, or an unsafe behavior), a video alert is sent directly to supervisors. This eliminates the need for manual investigations and ensures incidents are addressed immediately with visual proof. 2. Dynamic Coaching & Accountability. Supervisors can review incidents with operators in real-time, helping them understand what went wrong and how to improve. And use an AI chat assistant to guide coaching conversations and create customized coaching plans. 3. Standardized Training & Performance Monitoring. Allows warehouses to standardize safety coaching and performance training across multiple locations. It tracks leading indicators of unsafe behaviors and provides insights into operator performance trends, ensuring ongoing improvement. 4. Data-Driven Decision Making. The system compiles all coaching interactions into detailed analytics dashboards and employee scorecards for real-time insights into individual performance. Supervisors can identify high-risk employees, recurring issues, and areas needing additional training. But why does employee coaching even matter? Instead of reacting to accidents, a WarehouseOS allows warehouse teams to coach proactively, reducing safety risks and preventing incidents before they happen. And it helps create a warehouse safety culture that actually works–with a bunch of positive, cascading benefits. Operators receiving personalized coaching based on real-time data and video of what actually happened (and why), leads to fundamentally changing habits and behaviors in warehouses that the logistics industry has been trying to improve for a long time.
5. Continuous Improvement
Continuous improvement in warehouse operations is all about identifying inefficiencies, reducing risks, and optimizing processes to drive long-term success. And that’s exactly what our WarehouseOS aims to achieve at every level of your operation. 1. Proactive Safety & Risk Prevention. Stop accidents before they happen by detecting safety risks early, delivering real-time video for coaching and corrective action. Supervisors can now train teams with real-time insights according to your company’s coaching policies, ensuring consistent coaching across locations. 2. Process Optimization for Peak Performance, Even During Peak Season. A WarehouseOS goes beyond tracking—it analyzes workflows to eliminate wasted time. And it removes the guesswork—a WarehouseOS turns data into actionable next steps for continuous improvement. 3. Smarter Decisions with AI-Driven Insights. All operational data is compiled into customizable dashboards in a single platform, helping leaders track performance, compare sites, and roll out best practices. With automated reports and video proof, training and SOPs improve continuously. But you’re not doing this alone. AI chat functionality helps to analyze and serve insights without needing to be a data expert or requiring IT.
Beyond Software: Choosing the Right Partner
Selecting the right WarehouseOS is not just about purchasing software that has a bunch of features—it’s about finding a trusted partner who is invested in your long-term success.
The right warehouse technology provider should be more than just another vendor; they should be an extension of your team, committed to your success.
A true partner doesn’t just sell a system and walk away. From the very first conversation and throughout the partnership, they’re engaged and aligned with your business objectives.
Look for vendors who take the time to understand your business. They should assess your operational challenges and long-term goals before recommending if their solution is right for you (because sometimes warehouse technology like a WarehouseOS isn’t a good fit for everyone).
At OneTrack, we take a strategic partnership approach rather than a simple vendor-customer relationship. You’re not just buying warehouse technology, you're gaining a long-term ally vested in your success.
Also, evaluate a vendor’s experience, reputation, and ability to deliver results by considering case studies and testimonials from companies like yours with similar operations.
​
If you’re looking to accelerate your operations–while improving workplace safety, labor productivity, and shipment quality–then you need a WarehouseOS provider that’s prepared to grow with you.
​
But like any warehouse technology investment, a WarehouseOS isn’t just about features and who you do business with, but it also comes down to cost and ROI.
The ROI and Financial Benefits of a WarehouseOS
Investing in a WarehouseOS is not just about the upfront cost—it’s about the ROI it delivers over time.
​
While the total cost of ownership includes software, implementation, and field services, a well-designed WarehouseOS drives significant cost savings, productivity gains, and long-term operational improvements that far outweigh the initial investment.
​
From improving worker safety (which is priceless), productivity, decision-making, and customer satisfaction, understanding these measurable financial and operational gains is key to evaluating the true value of your investment.
By focusing on both tangible and strategic benefits, you can confidently invest in a WarehouseOS, knowing that it’s not just a cost—it’s a growth accelerator.

Chapter 6
How to Get Buy-In for a WarehouseOS
We get it—investing in new warehouse technology is a big decision.
But a WarehouseOS isn’t just another flashy tool; it’s a proven and scalable technology that simplifies warehouse operations, reduces costs, and makes life easier for everyone.
​
For example, companies using OneTrack’s WarehouseOS have seen impressive results, including:
By the Numbers
60%+
fewer damages
80%+
fewer incidents
10%+
productivity gains
Those numbers add up to serious cost savings and added value.
​
With improvements in safety, productivity, and shipment quality all from a single platform, you’re not just streamlining operations—you’re creating the gold standard warehouse operation.
A WarehouseOS is a smart investment.
But like any purchase, there’s a cost.
At OneTrack, we offer a simple, transparent pricing model designed to scale with your operations. We don’t believe in selling you more than you need. So whether that’s 20 sensors or 2,000, we’re flexible and configurable, making it easy to implement across your organization.
And the results are immediate–bringing critical visibility and accountability on Day 1.
So when you present leadership with the numbers and show workers how it makes their job safer, getting buy-in becomes a lot smoother.
Implementing the OneTrack WarehouseOS has led to significant ROI for companies, primarily through improvements in safety, productivity, and quality.
Here are some notable examples.
Chapter 7
OneTrack WarehouseOS Case Studies
A WarehouseOS isn’t just an operational upgrade—it’s a strategic investment that pays for itself through safer workplaces, higher productivity, and improved shipment quality.
Here’s what that looks like for OneTrack customers.
Chapter 8
The Future of Warehousing Starts with a WarehouseOS
The warehousing industry is at a crossroads.
With rising customer expectations, increasing operational complexity, and relentless pressure to improve efficiency, traditional warehouse management approaches are no longer enough.
The future belongs to those who embrace visibility and data-driven decision-making.
And a WarehouseOS is the key to unlocking that future.
​
Through safety, labor productivity, shipment quality, fleet management, and continuous improvement, a WarehouseOS turns your warehouse into a gold standard operation that’s safer, more productive, and more profitable.
No more guesswork. No more reactive problem-solving.
Instead, get full visibility that puts you in the drivers seat of your operations.
Companies that invest in the right warehouse technology today will lead the industry tomorrow.
So the choice is clear: stay stuck in outdated processes or take the next step toward a future-proof warehouse.
Take the Blindfold Off Your Warehouse Operations
You’ve seen how a WarehouseOS can drastically improve safety, productivity, and shipment quality–with impressive results.
Now it’s time to experience it for yourself.
Schedule a live demo of the OneTrack WarehouseOS and see firsthand how real-time visibility can fundamentally change your operations from day one.
Request a Demo Now and start building the warehouse of the future today.