Take the Blindfold Off Your Warehouse Operation
Get a Demo
Blake Martin
Director of Engineering, CJ Logistics
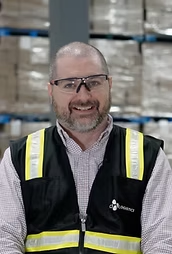
"You can't be everywhere and you can't see everything. The visibility OneTrack provides is critical and the ROI is immediately there. The technology works and the visibility allows you to improve all aspects of your business."
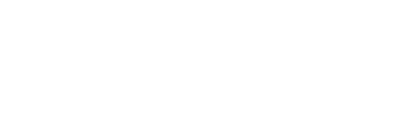
Top 100 Global 3PL
40+ OneTrack sites
Partner since 2019
The Challenge: Managing Performance Across 40+ Sites Left Blindspots
‍
CJ Logistics began their partnership with OneTrack at a single site back in 2019 to gain critical visibility into their workforce safety.
‍
“Prior to OneTrack, we were always looking reactively into a situation through witness statements and security cameras to try and rebuild what happened. But that was time consuming, and very difficult to do consistently and accurately and we wanted to become more proactive with our safety”
Joe Smiesko
VP of Safety, Security, and Compliance, CJ Logistics. Â
And after building an innovative safety program, they’ve now expanded to more than 40 sites across North America using OneTrack and quickly found there was an opportunity to further the value they bring to customers by transforming their labor management with video and AI.
‍
“We have wanted to move beyond engineered labor standards for a long time toward something that’s more holistic, but the tools and software we used could never get us there. It would take a lot of man hours in spreadsheets but we still felt like we weren’t getting the full picture”
Blake Martin
Director of Engineering, CJ Logistics.
‍
The Solution: NextGen Labor Management Using the OneTrack WarehouseOS
With the OneTrack WarehouseOS, CJ Logistics has one system to monitor people, processes, and product across their network so they can make improvements to safety, productivity, and quality.
Not only have they created a better overall culture and improved the customer experience but they’ve been able to make significant improvements to their productivity, increasing UPH by 11% on average across their network.
‍
“For us, productivity is all about keeping people on task, consistent, and removing any roadblocks for our employees. OneTrack has brought complete visibility into our processes and how we coach on performance, bringing insights we’ve never had before to better manage our labor productivity”
Laura Adams
SVP of Technology, Engineering, Systems & Solutions.
‍
‍
How CJ Logistics uses OneTrack to Improve Safety, Productivity, and Quality Across Their Network
- Combining WMS data and labor goals set within OneTrack to receive shift summaries of the top 3 most help needed employees along with video context to help with coaching.
- Dynamic dashboards to track every aspect of their labor productivity and performance, along with prescriptive insights to help eliminate bottlenecks.
- The ability to visually track and trace product at every touchpoint for enhanced shipment quality, transparency, and customer satisfaction.
‍
"When you have eight different systems, emails flooding in and phone ringing off the hook it’s easy to only focus on what’s the loudest. Whereas OneTrack gives us a holistic view of our buildings, not just with safety, productivity, and quality, but also for building set-up, for employee engagement. And that full picture helps us make decisions about where to put our resources most effectively".
Blake Martin
Director of Engineering