Take the Blindfold Off Your Warehouse Operation
We’ve talked before about the importance of developing a critical eye in your warehouse — using OneTrack video events as a window to what’s really going on so you can find additional coaching opportunities.
By looking for leading indicators of MHE safety events, you can spot patterns and coach operators to break bad habits before they become safety events.
But what does this really look like in practice?
Let’s take an in-depth look at a few real world examples captured in the OneTrack system.
Things to look for and how to coach forklift operators
As a refresher, here are the top leading indicators of MHE safety events that we’ve found after analyzing millions of warehouse safety incidents. You can take a look at a breakdown of these here.
Lack of personal protection equipment
Unsafe driving behavior
Distracted driving
​Environmental factors
- Safety glasses
- Safety belt
- Hearing protection (if required)
- Safety harness (if required)
- High visibility vest
- ​Unsafe turning
- Aggressive stops
- Not looking in the direction of travel
- Both hands not on controls
- Clear dashboard around controls
- ​Headphones
- Scanner use
- Phone use
- Talking
- Typing into RF/computer
- Eating/drinking
- Vaping/smoking
- ​Pallets, debris, or cracks on floor
- No safety halo around lift
- Not looking at intersections
- Tight squeezes
All of these examples we’re about to dig into triggered because a safety event followed. Whether it was an impact, a bump, or aggressive driving.
But almost more important as knowing when something happens, is recognizing why an event happened.
This empowers you to shape your operator conversations differently with video evidence, create better training, and optimize onboarding processes for new operators. It helps to proactively identify these patterns so you can coach operators and change processes before a safety event ever occurs.
Want to hear how Holman Logistics uses OneTrack to coach forklift operators and ensure their warehouses are safe? Check out their story here. Â
Forklift safety example #1
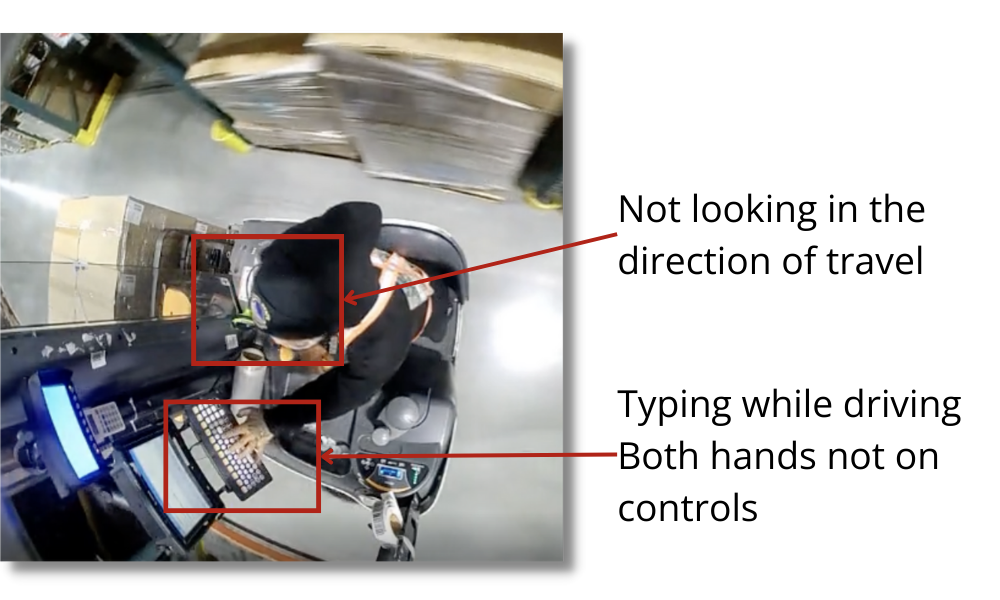
There are two main leading indicators to look for here:
- Not looking in the direction of travel
- Typing while driving, both hands not being on the controls
As tempting as it can be to multitask, there’s a lot going on in a warehouse and impacts can happen in a split second. Operators need to understand the importance of always keeping their eyes in the direction of travel, and using both hands when operating equipment.
Forklift safety example #2
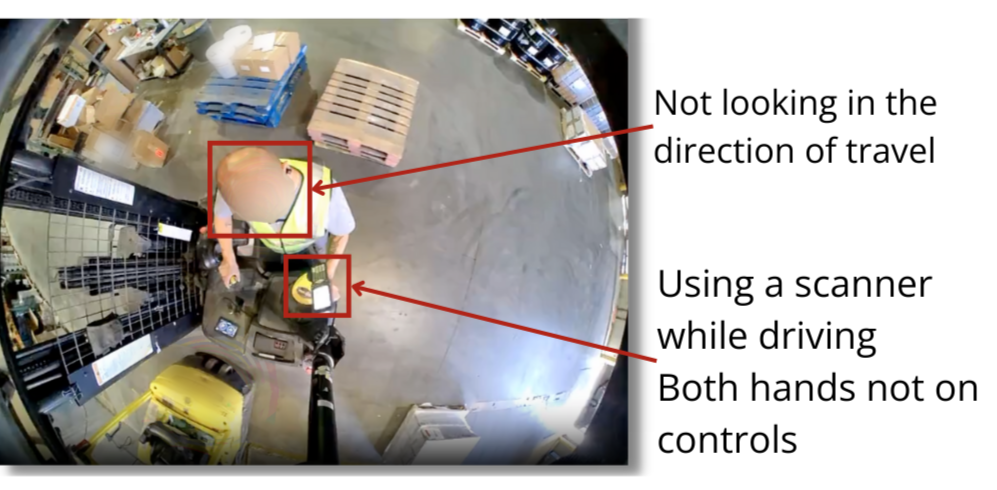
It’s important for supervisors to spend time reviewing event footage. If you don’t look for the right things, you can’t coach on the right things.
In this example there is:
- Not looking in the direction of travel
- Using a scanner while driving
- Both hands not on the forklift controls
Distracted driving is dangerous driving. A loose scanner can get stuck under the controls or easily fall inside or outside the lift.  A pedestrian could easily walk out in the way. A bump to a rack could cause a cascade of other issues like additional maintenance, early re-warehousing, product damages — not to mention injuries.
Lift operator best practice should always be to holster their scanner during operation, use both hands during operations, keep the dashboard clear of any tools and paperwork, and to clear any debris they see on the floor. Small habits can make a huge impact on warehouse safety.
Forklift safety example #3
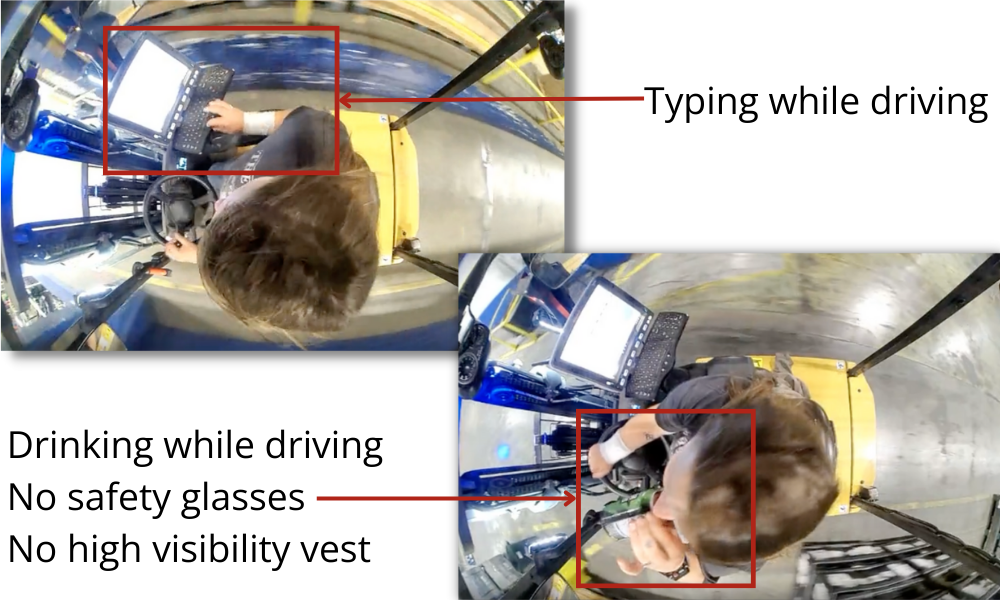
Several things to look for in this example:
- Again, typing while driving
- Drinking/eating while driving
- Not wearing PPE (glasses and high visibility vest)
We’ve talked about typing while driving, this takes the operators full attention off of operating the lift, it is very similar to texting and driving, and can be dangerous — the same goes for eating and drinking while driving.
When it comes to the lack of PPE, this is a very common leading indicator. But what happens when the glasses fall off the top of their head and they go to reach for them, taking their eyes off the environment around them? Or when something gets into their eye and obstructs their vision? Or when another worker doesn’t see that operator because they aren’t wearing a high visibility vest?
In all of these examples, the gut reaction is to think that these indicators are minor observations but the outcomes can be disastrous. Plus, without proper PPE, when an accident does occur injuries tend to be much more severe.
These behaviors need to be recognized proactively and coached before a safety event ever happens.
Example #4
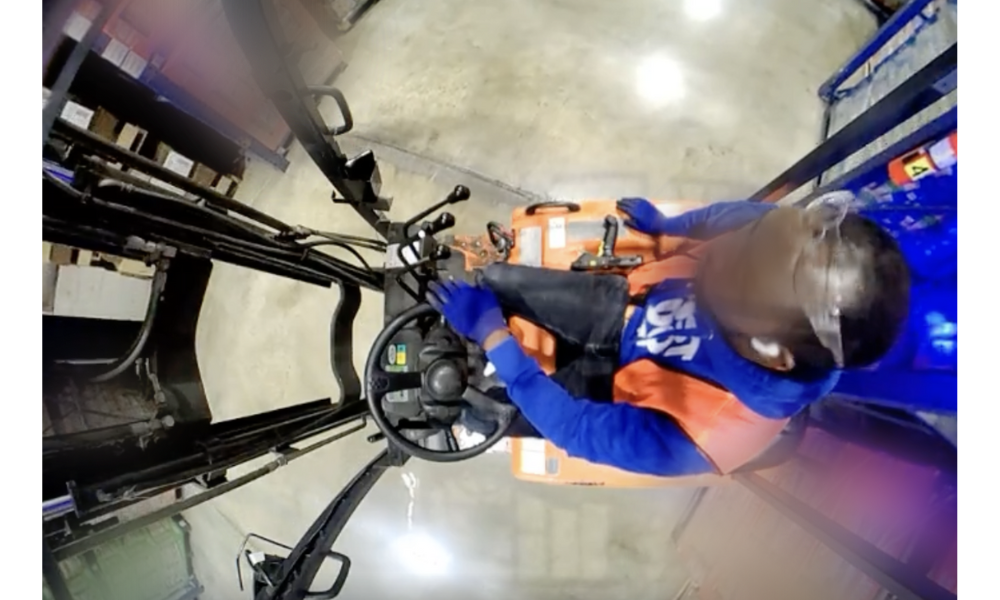
Now let’s take a look at an example that hasn’t been marked up yet.
What are the coaching opportunities here?
- This operator isn’t wearing their safety glasses
- They have AirPods in which can be a distraction and potentially against policy
- It doesn’t appear that their scanner is properly stowed
- One hand is resting on the side of the lift, leaving only one on the controls
This is a glimpse into what’s really happening on the warehouse floor. It’s an incredible opportunity to start changing the culture of your warehouse, create more awareness around the common causes of accidents, and help create more skilled forklift operators.
Using AI for proactive forklift safety is a massive opportunity to make sure that every employee gets home safe after each shift.
Want to see how you can upgrade your warehouse and forklift safety with AI? Learn more here.
‍