Take the Blindfold Off Your Warehouse Operation
Everything in warehouse operations is better with a plan, from forklift fleet management to preparing for peak season.
And warehouse safety is no exception.
After all, it's the number one priority among warehouse leaders.
Like Nick Watson, EHS Manager at Neovia Logistics, said on an episode of Warehouse Visionaries:
"My brain never shuts off on proactively changing processes and looking at the facility to ensure that we do everything in our power to make sure that someone doesn't get hurt…their safety is 100% my drive."
Ensure Every Warehouse Employee Clocks Out Safe After Every Shift
There's no denying that warehouses can be high-risk environments, with people and heavy equipment crossing paths across hundreds of thousands (or even millions) of square feet.
But keeping eyes on the warehouse floor 24/7 can feel like an impossible task. Because you can’t be everywhere all at once to know what’s really happening in your warehouses.
This leaves you blind to unknown risks and hidden hazards that can compromise the safety of your warehouse, and even cause you to be out of compliance with OSHA requirements (more on that below).
Ryan Donovan, President of States Logistics, shared on a webinar:
"I want all of our associates going home at the end of the day, the same way they came in, only happier because, at the end of the day, they've had a great shift, they've done their work, they're happy, they get to go home."
The ultimate goal is ensuring a safe working environment to help protect workers from accidents, injuries, or even fatalities.
But a safe warehouse not only minimizes risks, it can also improve productivity and employee retention. Because workers are more likely to stay with a company that values their safety and well-being.
And then there are compliance and legal obligations to consider.
Warehouses are subject to safety regulations and standards set by organizations like OSHA (Occupational Safety and Health Administration). And failing to comply can result in fines, penalties, and even operational shutdowns.
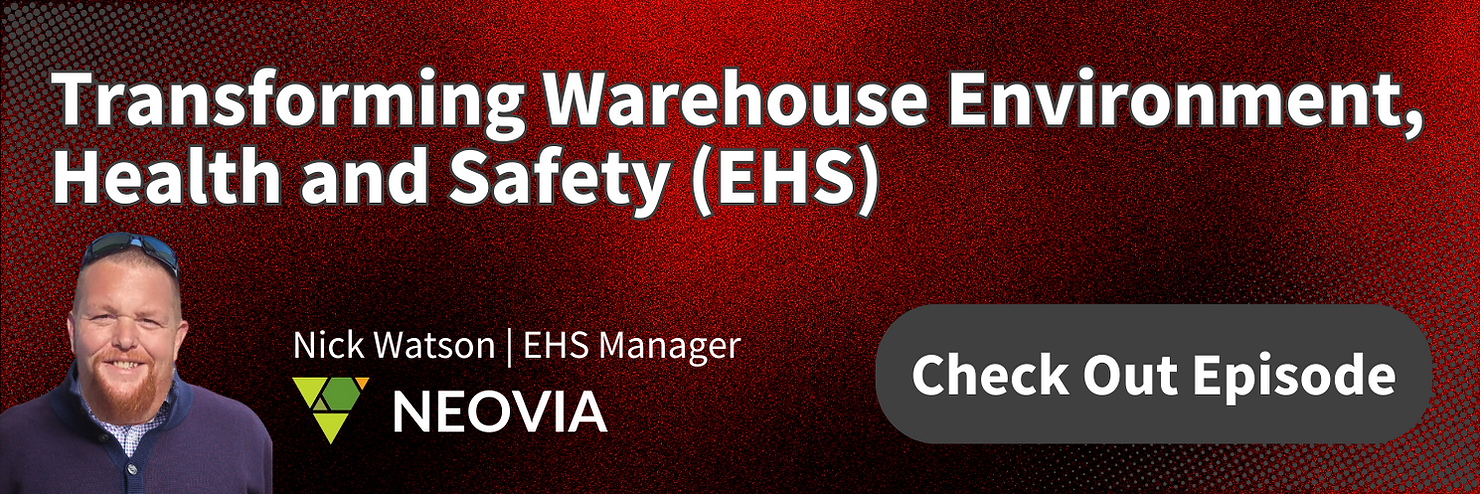
Why is Putting a Safety-First Focus into Practice so Critical?
Due to their complex environments with heavy equipment, high racking, and people performing (potentially) dangerous activities, warehouses are subject to strict OSHA standards.
OSHA inspections are aimed at identifying potential hazards and enforcing safety standards to prevent workplace accidents and injuries. According to a U.S. Department of Labor report:
The injury and illness rate in warehouses (5.5 incidences per 100 workers) is more than double the rate of 2.7 incidences per 100 for workers across all industries.
That’s a shocking statistic.
And one of several reasons why putting a safety-first focus into practice is so critical for every warehouse operation, including:
- Employee Safety: Ensuring the workplace is free from hazards reduces the likelihood of accidents and injuries.
- Legal Compliance: Helping operations avoid costly fines or penalties for non-compliance with safety regulations.
- Workplace Culture: Reinforcing a culture of safety and accountability which can improve employee performance and productivity.
We get it; OSHA might often be thought of as an annoyance. But they’re around for a reason.
To protect workers from hazards in the workplace and ensure safe working conditions
And at the end of the day, you know that you need to be compliant. And safety is a common cause that we can all support. But, many operations might be surprised to find out that their safety-first initiatives aren’t being reached to their fullest potential.
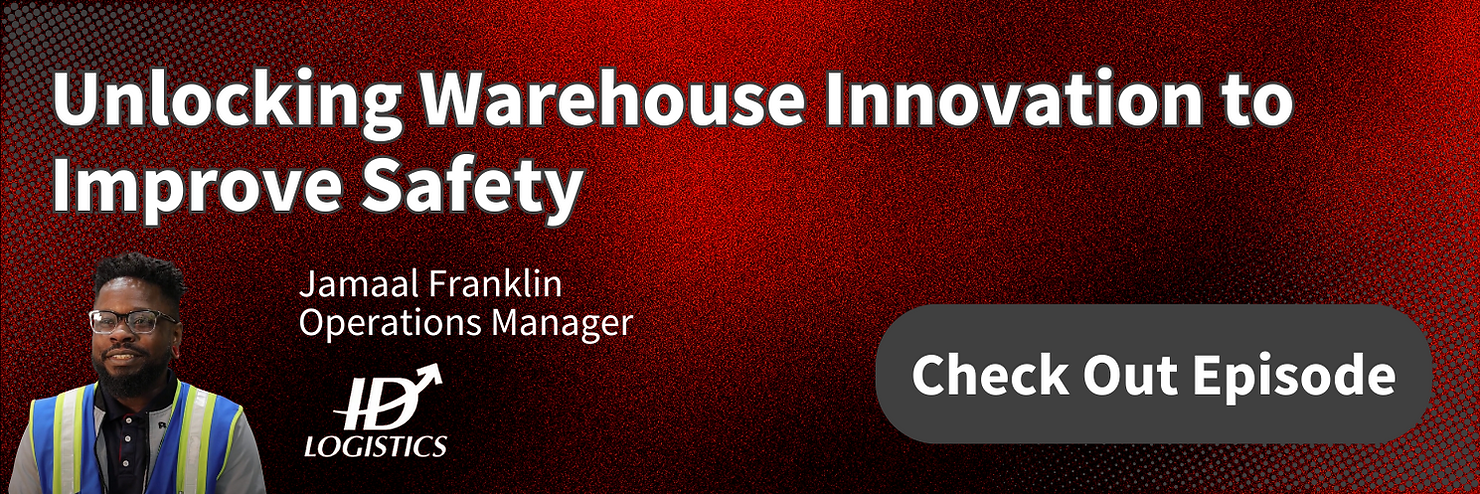
What are the Key Areas of Focus During a Warehouse OSHA Inspection?
OSHA inspections are usually a stressful time for warehouse owners and operators.
During an inspection, the warehouse will be checked for regulation compliance, common safety issues, equipment maintenance quality, employee training records, and more.
Forklifts and other material handling equipment (MHE) are always a focus of these inspections due to their high potential for injury. According to OSHA estimates, between 35,000 and 63,000 injuries occur every year involving forklifts, with 36% of forklift fatalities involving pedestrians.
Typically, you can also expect an OSHA inspection to cover the following areas:
General Housekeeping and Organization: Inspectors will check for proper organization and layout of the warehouse floor to prevent hazards leading to accidents and injuries. Worker training is a cornerstone of any good housekeeping program.
Storage and Stacking: OSHA inspections look for improper stacking or storage of materials, which can lead to tip-over hazards, falling objects, or even structural collapses. This includes ensuring heavy items are stored at lower levels and materials are correctly stacked.
Forklift and Material Handling Equipment: OSHA will check whether forklifts and other machines are properly maintained, if operators are adequately trained, and whether safety measures (such as seat belts) are used.
Personal Protective Equipment (PPE): Inspectors will check whether employees are using the necessary PPE, such as gloves, helmets, safety glasses, and steel-toed boots, depending on the risks in the warehouse environment.
Hazard Communication (HAZCOM): Warehouses must maintain safety data sheets (SDS) and proper labeling for chemicals and train employees on potential dangers when handling hazard materials.
Electrical Safety: Inspectors will review electrical systems, ensuring no exposed wires, proper grounding of equipment, and compliance with lockout/tagout (LOTO) procedures to prevent electrocution.
Emergency Exits and Fire Safety: Inspectors will ensure clear, unblocked emergency exits, proper signage, fire extinguishers, and fire suppression systems in place. They will also check that employees are trained in emergency evacuation procedures.
Lockout/Tagout (LOTO): Warehouses that use heavy machinery must have LOTO procedures in place to prevent accidental start-up of equipment during maintenance. OSHA will ensure that employees are trained in these procedures.
Fall Protection: Fall hazards, such as unguarded platforms, ladders, or mezzanines, will be closely examined. OSHA requires appropriate fall protection systems, like guardrails or personal fall arrest systems, to prevent accidents.
Ergonomics: Although OSHA does not have specific ergonomics standards, they will assess whether employees are exposed to repetitive stress injuries due to lifting, pulling, or other physical tasks. Proper techniques and equipment are expected to mitigate risks.
How to Prepare for an OSHA Inspection
Usually, OSHA conducts inspections without advance notice. But there are steps you can take now so you aren’t caught off guard by a surprise OSHA inspection; prioritize safety programs and warehouse safety checklists.
Conducting your own regular equipment inspections with safety checklists, along with the required pre-shift forklift inspections, is one way to always be prepared for unplanned OSHA inspections and maintain optimal conditions in your warehouse.
Here are 4 more tips to prepare your warehouse for an OSHA inspection:
- Regular Audits and Safety Walkthroughs: Warehouses conduct internal audits and safety walkthroughs to identify potential hazards before OSHA arrives. These inspections focus on areas like housekeeping, equipment maintenance, fire safety, and emergency exits.
- Employee Training: Ensuring employees are up-to-date with required safety training is critical. This includes forklift operator certification, hazard communication (HAZCOM) training, and personal protective equipment (PPE) training. OSHA inspectors often interview employees, so ensuring everyone is trained and aware of safety protocols is vital.
- Maintaining Documentation: OSHA requires proper documentation, such as injury logs, maintenance records, hazard communication programs, and employee training records. Warehouses should ensure all paperwork is accurate, updated, and readily accessible in case of an inspection.
- Pre-Shift Equipment Inspections: One key OSHA requirement is conducting daily equipment checks, particularly for forklifts, before each shift. Forklifts, as heavy equipment, are subject to detailed inspections to ensure they are in safe working condition.
Warehouse Safety Checklists: Key to Preparing for an OSHA Inspection
When it comes to OSHA inspections, there are generally two main types of inspections.
The first is programmed inspections, where OSHA must provide notice and strictly keep their inspections within that pre-defined scope. Factors that may lead to a facility being selected for a scheduled inspection include its citation history and incident rates.
The other is unprogrammed inspections, which are usually triggered by employee complaints, referrals, or reported accidents or incidents. Since OSHA’s primary goal is to correct hazardous workplaces, unprogrammed inspections are typically given priority over programmed inspections.
And to address increasing risk across warehousing (remember, the rate of illness and injury is more than double other industries), OSHA has put in place a National Emphasis Program (NEP) for the next 3 years. Inspections related to a NEP can be both programmed or unprogrammed, and the scope of the inspection is much broader than a regular inspection.
Before conducting an inspection, OSHA compliance officers research the inspection history of a site using various data sources and review the operations and processes in use and the standards most likely to apply.
What if you had digital records and data available at a moment's notice for an OSHA inspection and when conducting your own assessments?
Warehouse safety checklists are a simple but powerful tool you can use to identify potential hazards so you can then take corrective action and reduce or eliminate those hazards. This will help you improve critical operational areas that OSHA cares about and, most importantly, keep people safe.
By systematically checking for issues and ensuring compliance with safety protocols, warehouse safety checklists can help you:
- Prevent Accidents: A well-structured safety checklist helps identify potential hazards before they cause harm. By routinely checking equipment, workspaces, and safety protocols, employees can address issues before they escalate into accidents.
- Ensure OSHA Compliance: A checklist helps ensure all necessary protocols are followed, reducing the risk of non-compliance penalties.
- Protect Employees: Workers are the most valuable asset of any business. A safety checklist ensures employees have a safe work environment by identifying risks such as improper lifting techniques, unmarked hazards, or faulty equipment.
- Increase Efficiency: By systematically maintaining equipment and workflows, checklists help warehouses operate smoothly. Well-maintained machinery and properly organized spaces lead to fewer disruptions, downtime, and inefficiencies.
- Reduce Costs: Workplace accidents, machinery breakdowns, and non-compliance fines can incur significant costs. A safety checklist helps minimize these risks, saving a warehouse from financial losses due to medical bills, lawsuits, or damaged goods.
Here is a sample warehouse safety checklist for your safety inspections.
‍
Implementing and Maintaining Warehouse Safety Checklists
Most warehouses operate 24/7/365 to keep pace with an economy that never sleeps. Goods are constantly moving through the supply chain, with warehouse operators working around the clock to keep up with demand.
But when pressured to work faster, it’s important to not lose sight of safety.
Ryan Donovan put it this way, “We can never sacrifice on safety. We don't want to sacrifice safety for speed.”
Creating safety checklists is a good start to ensure that you don’t compromise safety for speed.
But its success depends on how well it is implemented and maintained. Here are some best practices to ensure the checklist becomes an integral part of your warehouse safety culture:
- Regular Audits: Conduct routine safety audits using the checklist to identify hazards and areas for improvement. These audits should be scheduled at regular intervals, such as daily, weekly, or monthly, depending on the risk levels of specific tasks.
- Employee Involvement: Safety is a team effort. Encourage employees to actively participate in safety checks and report hazards. Companies can create a culture of accountability and awareness by involving workers in safety initiatives.
- Continuous Training: Safety training should be ongoing and include new employees and regular refresher courses for existing staff. Training should cover how to use equipment, follow safety protocols, and respond in emergencies.
- Adapting to Change: Warehouse operations evolve, and so do the risks. Ensure the safety checklist is updated as new processes, technologies, or regulations are introduced.
- Use Technology: Digital checklists, integrated with warehouse management systems (WMS), can streamline safety audits and record-keeping. These systems can alert managers when equipment inspections are due or when a potential hazard is flagged, ensuring nothing is overlooked.
In addition, OSHA has a comprehensive forklift safety checklist available here. And also provides a few general safety precautions and best practices here to help keep your warehouse operating safely,
But keep in mind that when it comes to warehouse safety checklists, every warehouse will have different hazards depending on its size, layout, and the materials it stores.
So plan accordingly for your warehouse operations.
And every plan needs a place to start.
For our customers, that’s often pre-shift forklift inspections.
Where to Start: Pre-Shift Forklift Inspections
The potential for danger in a warehouse is high with people and machines sharing space in tight, fast-paced environments. Because of this, forklifts and other material handling equipment are a top area of focus for regulators. And represent the single largest category of safety citations for warehouses.
To avoid citations, OSHA requires all forklifts to be inspected by their operators at the beginning of every shift, and for any identified deficiencies (e.g. inoperable headlights, broken mirrors, etc.) to be corrected before those forklifts are operated. Violations of either of these processes can result in fines of over $10,000 per forklift.
In most warehouses, the inspection process is done on paper checklists. Like any paper-based process, this… has its shortcomings.
The completed checklists are frequently filed away in drawers never to be seen again, and managers cannot be sure which operators are actually completing their checklists or if any identified issues are actually being fixed.
On the other hand, a digital approach to safety checklists can:
- Provide real-time insights into equipment status, allowing managers to address issues immediately.
- Ensure compliance and make inspection records readily accessible during an OSHA inspection.
- Automate alerts for maintenance needs or failed inspections, ensuring no critical issues are overlooked.
- Track trends and identify recurring issues, enabling predictive maintenance and reducing downtime.
- Streamline the inspection process by reducing the time it takes to record and store information, and complete inspections more efficiently.
Warehouse operators should weigh the pros and cons of each method based on their size, budget, and operational needs to ensure they are well-prepared for OSHA inspections and overall safety management.
Best Practices for Pre-Shift Forklift Inspections
Here are a few tips to get the most out of your pre-shift forklift inspection:
- Consistent Routine: Whether using paper or digital methods, ensure that pre-shift inspections are consistent, with operators inspecting the same components each time.
- Employee Training: Properly train operators on how to conduct forklift inspections. This includes identifying potential issues and understanding the importance of reporting them.
- Address Issues Immediately: If an issue is identified during an inspection, it should be addressed before the forklift is used. This can prevent accidents and ensure OSHA compliance.
- Review Records Regularly: Periodically review inspection records to identify trends and recurring problems. This proactive approach can improve safety and reduce equipment downtime.
For warehouses looking to maintain peak performance, implementing and regularly updating safety checklists is critical to being prepared for surprise OSHA inspections.
Here is a sample safety checklist for your pre-shift forklift inspections.
‍
Digital Pre-Shift OSHA Inspections and Impact Monitoring with OneTrack
With OneTrack, stay OSHA compliant with new safety checklists. Go from paperwork and clipboards to creating and managing configurable checklists for your sites all in a single Warehouse Operating System. And link equipment to checklists, access them via your mobile device, and search previously submitted checklists by customer, plant, and machine.
So now through your tablet or mobile device, operators can complete their pre-shift inspection checklist. If an issue is identified, maintenance personnel are notified and operators receive audio and visual alerts when they operate a forklift without completing their inspection.
And to track progress, warehouse management can access live reports detailing how often their forklifts are being operated outside of OSHA compliance.
A major 3PL that adopted OneTrack experienced the benefits of this digital shift first-hand. When our Warehouse OS was first installed, they learned that pre-shift checklists at one of their facilities were only being completed 40% of the time - a problem they were not aware of before.
With the digital data collected from OneTrack in hand, the 3PL’s facility management implemented new policies, re-trained their operators, and saw immediate improvement. Within four weeks, pre-shift inspection checklists were being completed over 99% of the time.
They now monitor checklist compliance on a daily basis, ensuring their lifts are being operated in a safe, OSHA-compliant manner.
To see if OneTrack is a fit for your forklift fleet, reach out to us to schedule a time to talk.
‍