Take the Blindfold Off Your Warehouse Operation
OneTrack Guide
The Warehouse of the Future
Everyone talks about âThe Warehouse of the Futureâ, but most warehouses donât even feel like 2005, much less 2025.â
Walk into the average warehouse, what do you see?
Hundreds of thousands of square feet, racking to the ceiling filled with product, and pedestrians and machinery flying around trying to get orders out the door â all orchestrated based on timestamps, stacks of paperwork and spreadsheets, and a web of siloed software that would make anyoneâs head spin.Â
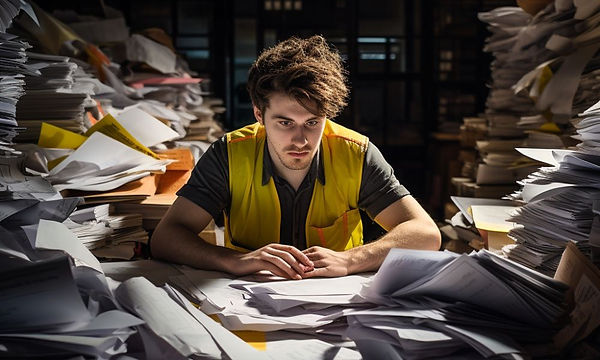
Good data is hard enough to access, not to mention getting engineering or IT resources to then actually analyze it. Unfortunately, that leads to most warehouses putting out the hottest fire head-on, one at a time, instead of using data to get ahead.Â
Unreported safety issues run rampant with limited accountability. Performance KPIs start slipping but no one really knows why, so youâre left telling employees to work faster based on what a spreadsheet says. And product damages and OS&D claims start piling up, losing you money and damaging your reputation.Â
Something is missing: visibility into your people, processes, and product â all backed by data that doesnât take an army of engineers to make decisions with.Â
So before you can scale automation, robotics, and AI (all things that most people think is the future of warehousing), you first need complete visibility into your warehouses. Thatâs how you build the Warehouse of the Future â and weâve put together this blueprint to help you do it.
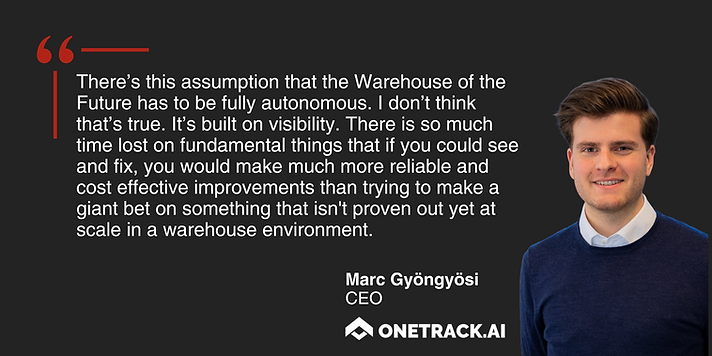
â
What is the Warehouse of the Future?
The Warehouse of the Future isnât just a building, itâs a hub of real-time visibility and AI-driven decision making in your operations so you can improve safety, labor productivity, and shipment quality.
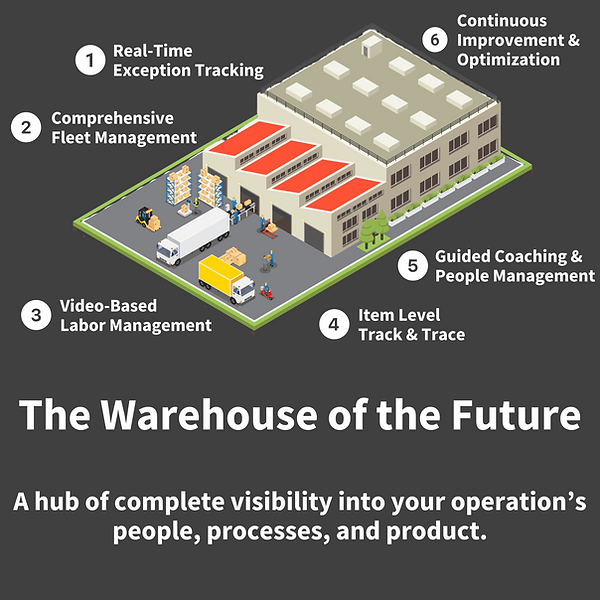
1. Real-Time Exception Tracking
Status Quo
Everyday countless exceptions happen in your warehouses that go unseen and unreported.Â
From phone use violations, impacts, unsafe behaviors, low productivity, and shipment quality issues â all costing you time, money, and risking worker safety.
We all intuitively know that these issues occur, but without full visibility into why itâs happening, itâs a struggle to understand the root cause and fix the problem at its core, hold people accountable, and drive the right behaviors throughout your organization.
Warehouse of the Future
Itâs impossible to keep eyes on everything happening in a warehouse 24/7 â or is it?
With a combination of AI and computer vision, that level of visibility is possible.
Top 3PLs, shippers, and manufacturers are getting real-time video alerts after every exception across people, product, and processes in their warehouses.
Coupled with guided next steps for proper coaching and prescriptive analytics for root cause analysis and continuous improvement â you can spend less time investigating exceptions and more time improving operations. Â
"There are so many hidden hazards in a warehouse. With the visibility we have now, itâs been a huge eye opener for us. Things we would have never known about otherwise weâve been able to identify and create policies to help keep people safe and productive."
Melody Moore
Director of Quality & EHS
Watch Podcast Episode
â
2. Comprehensive Fleet Management
Status Quo
How many pieces of equipment are in your warehouse? What about across your network? 50? 100? 1000? How many of those do you actually need to keep your operation running smoothly?
Sure, traditional telematics can get you part of the way there but thereâs some major blind spots. Truth is, most leaders canât answer the first question, much less the second. That means serious money is left on the table.
Warehouse of the Future
The Warehouse of the Future isnât just about automation and AGVs. No matter what type of equipment is used in your warehouse â you still need to know how much equipment you actually have, and if itâs the right amount for the job.
You need a way to get detailed utilization data on every piece of equipment in your fleet. From how much time is spent driving, sitting idle when itâs supposed to be moving, and how long equipment isnât being used. All with predictive insights to let you know where you can right size your fleet and save money without sacrificing performance.
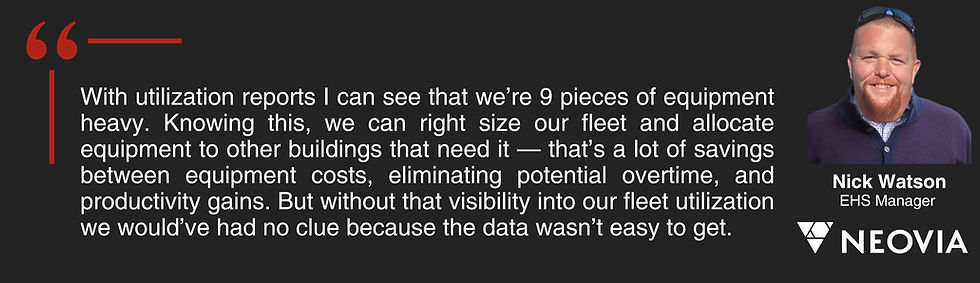
3. Video-Based Labor Management
Status Quo
Youâre trending behind your performance goal, but why?
Your WMS and LMS are just a record of when and what, leaving you completely in the dark for the why and how. Without it, youâre left telling employees to work faster based on numbers in a spreadsheet which leads to higher turnover and a âno man's landâ of performance and culture.
Warehouse of the Future
Imagine, instead of combining through transaction line items and timestamps, your system automatically flagged whenever you started falling behind goal, and sent you video evidence of your most help needed employees and slowest transactions so you could proactively see the root cause of your productivity dips and get ahead of them.
Thatâs the labor management program for The Warehouse of the Future.
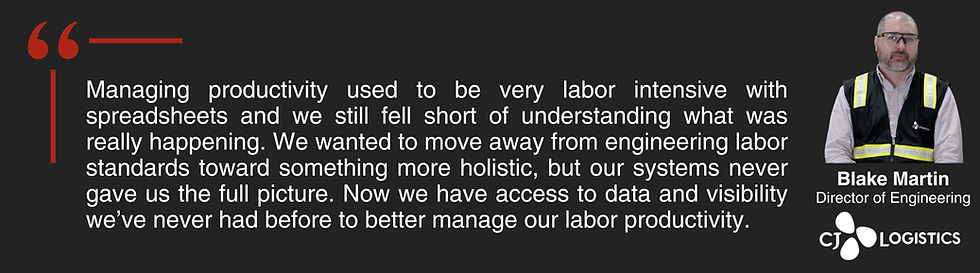
â
4. Item Level Track & Trace
Status Quo
Billions of dollars of product moves through warehouses all over the world every day. Each time that product is touched is a chance for damages or a mistake that costs you money and can damage your reputation with your customers.
But every touchpoint is just captured by a barcode scan with no visibility to the actual product or its location. And every shipment leaving the warehouse could be a potential OS&D claim with no way to validate it.
Warehouse of the Future
The Warehouse of the Future will be built on visibility at every level and every scan
Every time a product is moved, you should get a corresponding picture or video showing you exactly what happened, where it happened, and what condition the product was in.
From the moment it leaves the manufacturing line, to when itâs putaway, picked, then shipped back out â and everything in between â shipment quality is automatically validated.
"We used to have to take pictures of loads to show nose, middle, tail, but that only shows so much and was a huge productivity killer. Now weâre recording the entire load process and sharing with the customer to prove their product quality is at the top of our priority list."
Joe Labrosky
Distribution Center ManagerRead Case Study
â
5. Guided Coaching & People Management
Status Quo
Employee information. Equipment certifications. Corrective Action. Performance reviews. All stored in separate binders, or at best, an HR software that no one else has easy access to.
That makes it nearly impossible to manage your most important asset in a warehouse: your people.
Supervisors struggle to maintain consistent coaching conversations, certifications become outdated, and top performers leave because they donât want to wait for the promise of a performance review that never comes to receive recognition for their hard work.
Warehouse of the Future
Imagine never having to hunt for employee information again.
What if everything you needed to manage your team was right at your fingertips, delivered in real-time, exactly when you needed it? From customized coaching policies to hold supervisors and operators accountable, to comprehensive performance records covering safety, productivity, quality, and equipment certificationsâitâs all there.
And add in automated coaching in the critical moments that matter most without ever leaving your desk. Thatâs the Warehouse of the Future.
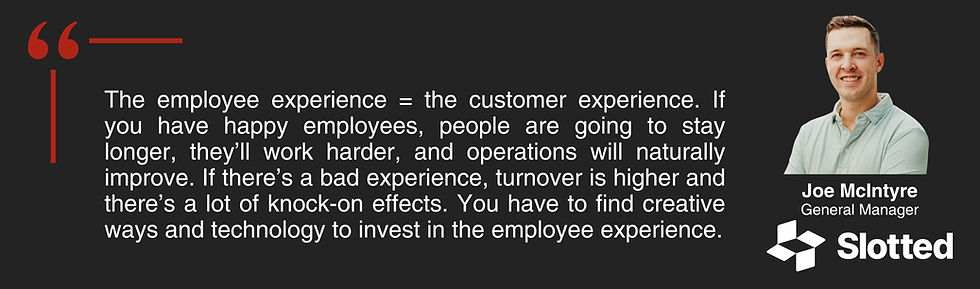
6. Continuous Improvement & Optimization
Status Quo
Continuous improvement is a cornerstone of nearly every warehouse operation on the planet.
But achieving it often means relying on scarce engineering resources for tasks like time studies, engineered labor standards, spaghetti diagrams, heatmaps, layout planning, and pick-line optimizationsâthe list goes on.
The reality?
Skilled engineering talent comes at a premium and is hard to secure. And even then, theyâre often working with imperfect data, leaving significant improvement opportunities untapped.
Warehouse of the Future
The Warehouse of the Future isnât held hostage by inaccessible data or reliance on engineering resources wasting countless hours spread across eight systems and buried in a dozen spreadsheets
Instead, the Warehouse of the Future operates on a unified WarehouseOSâbringing all your data together in one place, seamlessly synced with video context, and proactively highlighting opportunities for continuous improvement and optimizationâno extra analysis or engineering resources required.
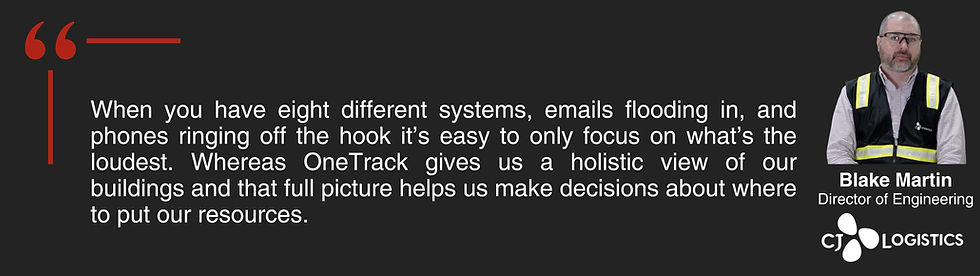
What is Holding People Back?
Itâs a mix of hurdles creating a cycle that keeps warehouses stuck in survival modeâreacting to problems instead of making meaningful progress toward innovation.
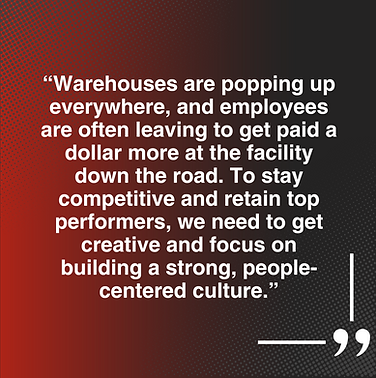
A cycle of employee turnover
Turnover remains one of the biggest hurdles in logistics, creating a domino effect of challenges.
The cost of hiring labor and employee training strains budgets, while a revolving door of workers leads to productivity inefficiencies and safety exceptions. Itâs impossible to build a world-class safety culture without a consistent team.
Instead of focusing on innovation and progress toward the Warehouse of the Future, youâre stuck treading waterâbeing reactive instead of proactive.
â
â
â
â
â
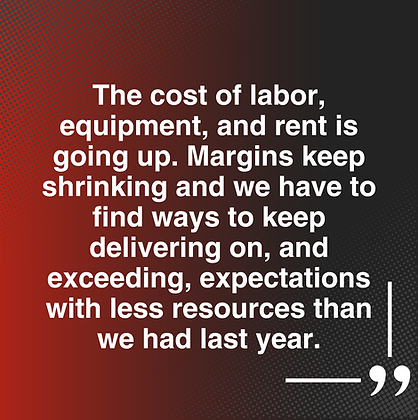
Tighter margins & budgets
Shrinking margins force budgets to tighten, perpetuating a vicious cycle.
Limited resources make it harder to retain employees, amplifying turnover issues (see above). At the same time, reduced budgets mean fewer opportunities to invest in the technologies necessary to support your overall supply chain strategy.
The result?
Progress stalls, and challenges compound.
â
â
â
â
â
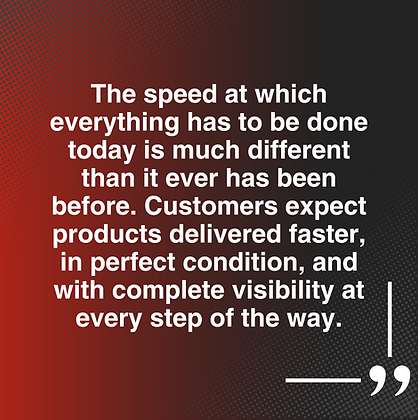
Racing to meet expectations
Two-day shipping. One-day shipping. Same-day shipping! Speed is no longer a perk; itâs the baseline expectation.
However, balancing the need for speed with quality, safety, and labor retention is a constant struggle.
Cutting corners to meet goals can damage customer relationships and hurt workplace culture.
Stretched resources lead to process breakdowns, leaving you stuck in survival mode instead of building a strategic, future-focused operation.
â
â
â
â
â
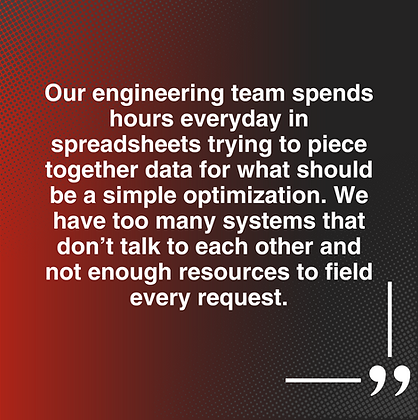
Disjointed systems
No two warehouses operate exactly alikeâeven within the same organization or network, every warehouse has unique people, systems, and processes.
Not to mention having multiple systems, spreadsheets, and stacks of paperwork to sort through.
This chaotic âfrankenstackâ of solutions makes it nearly impossible to gain a holistic view of operations so you can move beyond the status quo and achieve the Warehouse of the Future.
â
â
â
â
â
The Path Forward
The biggest obstacle to building the Warehouse of the Future is a lack of visibilityâwithout visibility into people, processes, and product, itâs impossible to build the Warehouse of the Future.
You canât solve problems you canât see. The #1 thing holding most operations back is a lack of visibility.
Want to decrease turnover?
You need to understand why people are leaving and create a culture of trust, transparency, and accountability. But you canât do that if safety exceptions are running rampant and youâre coaching productivity based on timestamps and spreadsheets.Â
Want to be more profitable?
Start by identifying where revenue is slipping away. Lost time to shift changes, long-running breaks and lunches, or indirect time. As well as right sizing your fleet based on in-depth utilization data, reducing OS&D claims with item-level track and trace, and massive savings from fewer product damages and safety events by implementing effective behavioral coaching.Â
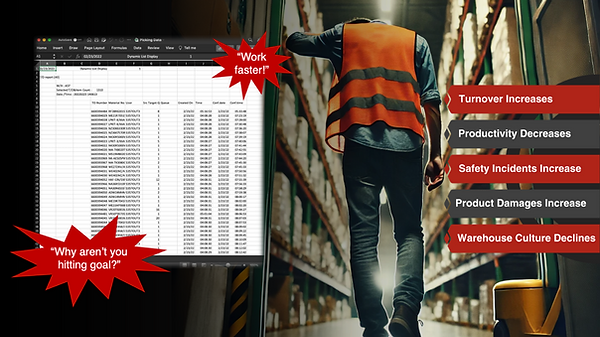
Need to speed things up without sacrificing safety or quality?
It starts with being able to see your current bottlenecks and most help needed employees. Just from that weâve seen customers increase UPH by more than 10% on average across their network.
All this visibility is possible with a single Warehouse Operating System (WarehouseOS).
It combines your legacy systems (like your WMS), digitizes and automates core processes (such as safety investigation or pre-fligh inspections), and delivers prescriptive, data-driven insights straight to your inbox. No need to dig for information or have an army of engineers analyze dataâ youâll always know where to focus resources for maximum impact.
Bottom-line?
Itâs not easy to make the changes necessary to make the Warehouse of the Future a reality today, instead of a distant day dream. It takes commitment at all levels to change the way you approach people, processes, and products in your warehouses. If you want world-class operations you canât keep doing things the same old way.
â
Building the Warehouse of the Future Takes Vision...Computer Vision
Operations, inventory, EHS, engineering, 3PL, brand, shipper â weâre all in this together. Logistics is at a breaking point. The status quo wonât cut it anymore but the Warehouse of the Future doesnât have to be years away. You can start now.Â
Visibility is the missing ingredient and a WarehouseOS is how you put it to work in all aspects of your operation.
OneTrack is the WarehouseOS that brings complete visibility to people, process, and product within warehouses. By combining proprietary AI camera sensors, real-time video alerts, and customizable analytics, companies like Kellanova, Ryder, and ID Logistics have lowered safety incidents by more than 80%, improved productivity over 10%, and reduced damages by 60%.
â
Success Story
See How This 3PL is Building the Warehouse of the Future
Learn how Holman Logistics, a leading 3PL, is using the OneTrack WarehouseOS to gain visibility into their people, processes, and product