Take the Blindfold Off Your Warehouse Operation
‍PLAYBOOK
How to capture load quality and validate OS&D claims (Automatically)Â
“That shipment we just got has damages”.
How often do you get that call from a customer or end delivery location?Â
Trailer returns are pricey, frustrating, and if you’re a 3PL and your customer is blaming you, that could mean losing a customer.Â
Ever wish you could quickly search that order and see exactly what happened?
Whether it’s for continuous improvement or simply proving that the product left your warehouse in great condition, you need better visibility into the entire loading process to get ahead of potential OS&D issues.Â
That’s where this playbook comes in. Let’s break it down.
How it works
Set up a process to record every loadÂ
Quickly search an order number to investigate load quality
Do regular spot checks for continuous improvementÂ
The Playbook
Step 1: Set up a process to record every single pallet you load onto a truckÂ
First things first you need a way to capture your load process. For some companies, pictures are where they start, for others video is more helpful.Â
We recommend video for a few reasons:
- Context is kingVideo will show you everything that happened. Not just what happened in one small part of a load.
- Video is easier to review. It’s much easier to sit down and watch a 3 minute video of a load rather than trying to piece together what happened based on a bunch of load proof pictures.Â
- You can set it on autopilot. OneTrack can connect to your WMS to automatically start recording based on the WMS data so your operators only have to worry about loading the truck, not taking pictures.Â
Our approach is simple. Take the same great overhead AI camera that we use for safety and productivity, mount it as a forward facing camera on your forklifts, and train the AI model to look for damaged product or missing pallets instead of safety or productivity events.
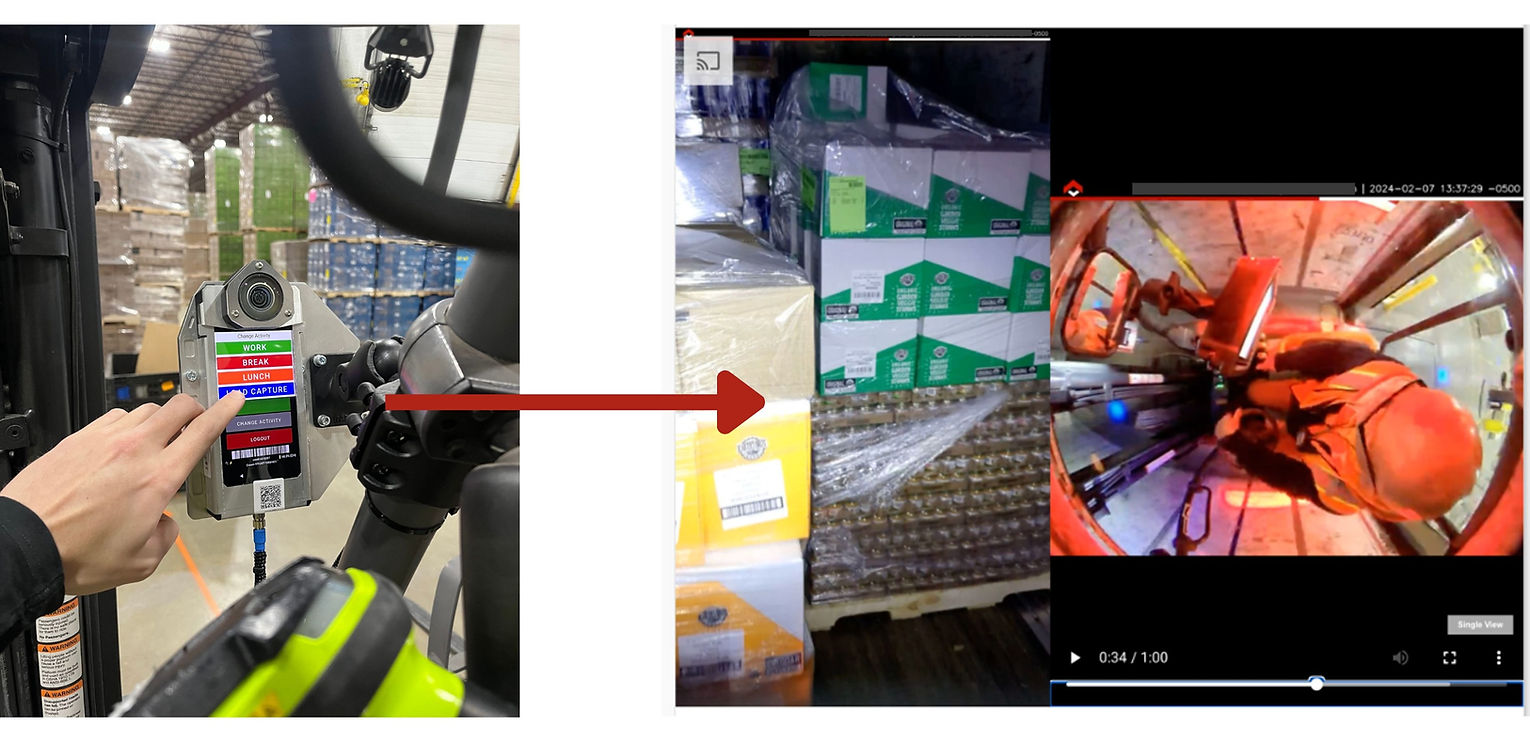
Once those are installed by our in-house field services team, you have two options on how to capture your loading:
- Operators can manually change into a “Load Capture” function directly on the sensor (like the above picture).Â
- We connect to your WMS to automatically capture the entire load sequence based on WMS timestamps (Most popular option).
If you're worried about how your I.T. team will react to a WMS integration project, don't be.
Here's what Carrie Ferrone, Manager, Business Process Analysis at ID Logistics had to say:
Step 2: Quickly search an order number to investigate the load qualityÂ
Now when you get that call about damages, here's what you do:
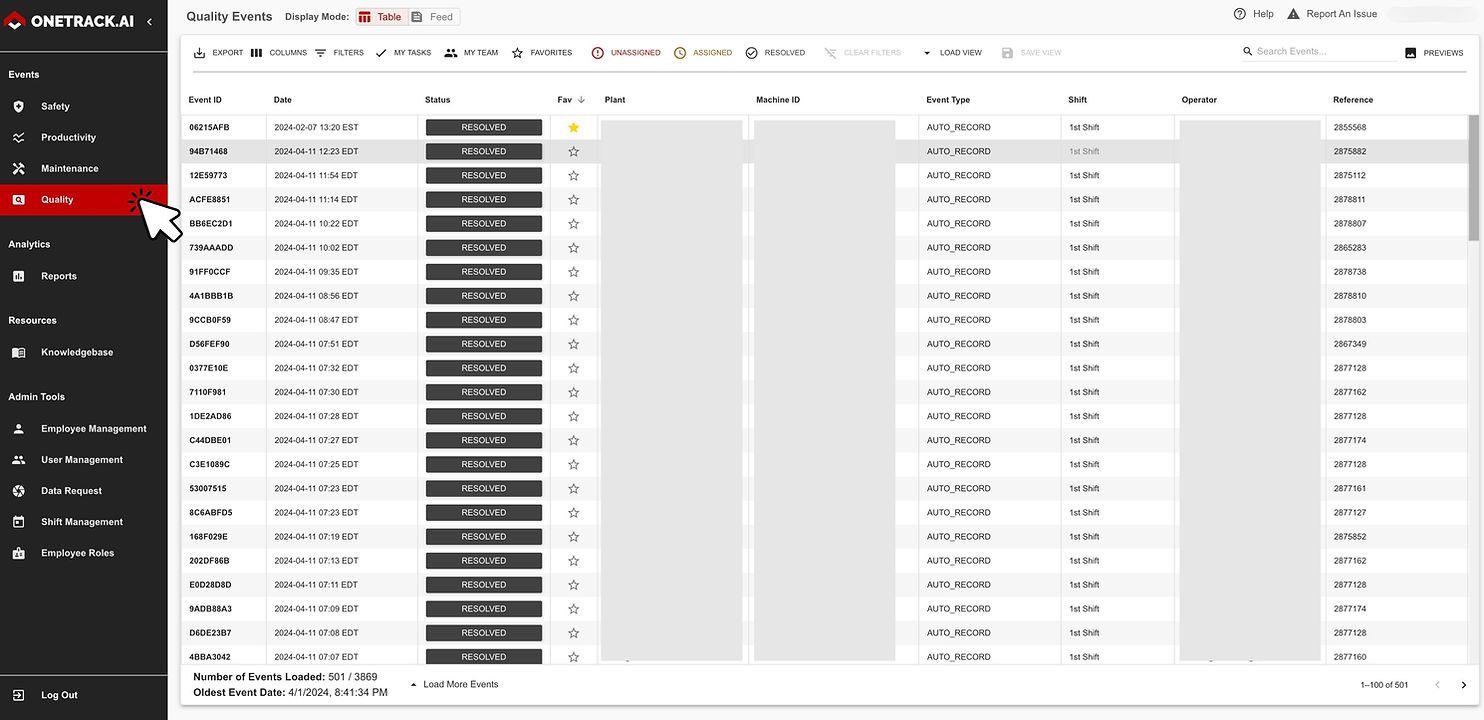
Hop into your OneTrack dashboard and then navigate to the Quality events section.Â
The first thing to note is all the way on the far right, you’ll see a reference column.Â
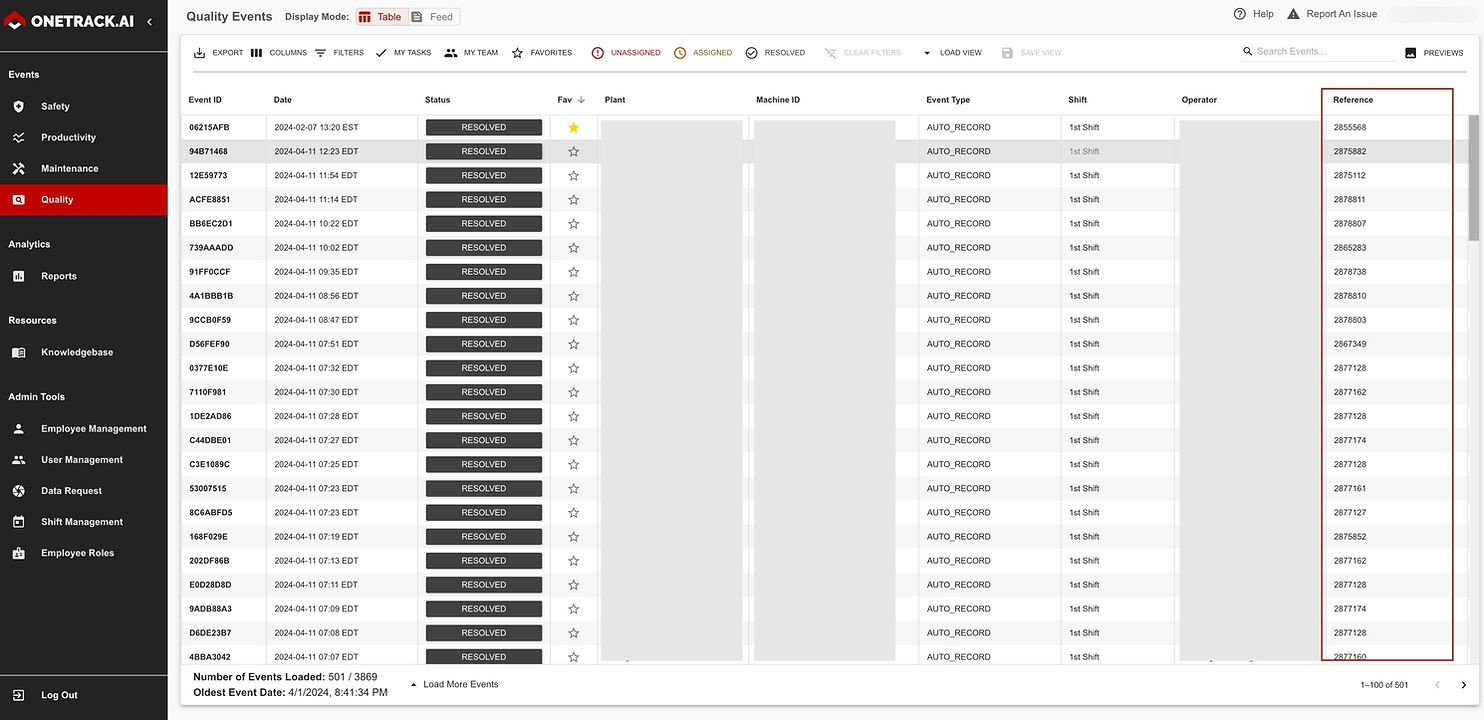
This is going to be your unique identifier for each load. It can be anything you want, but typically this is the order number from your WMS for easy reference.
You can quickly search for an order number and jump straight in for review.Â
When you click into the event you’ll see two camera views. One overhead of the operator and the other forward-facing view of the loading process. This gives you a complete picture of exactly what happened during the load in question.
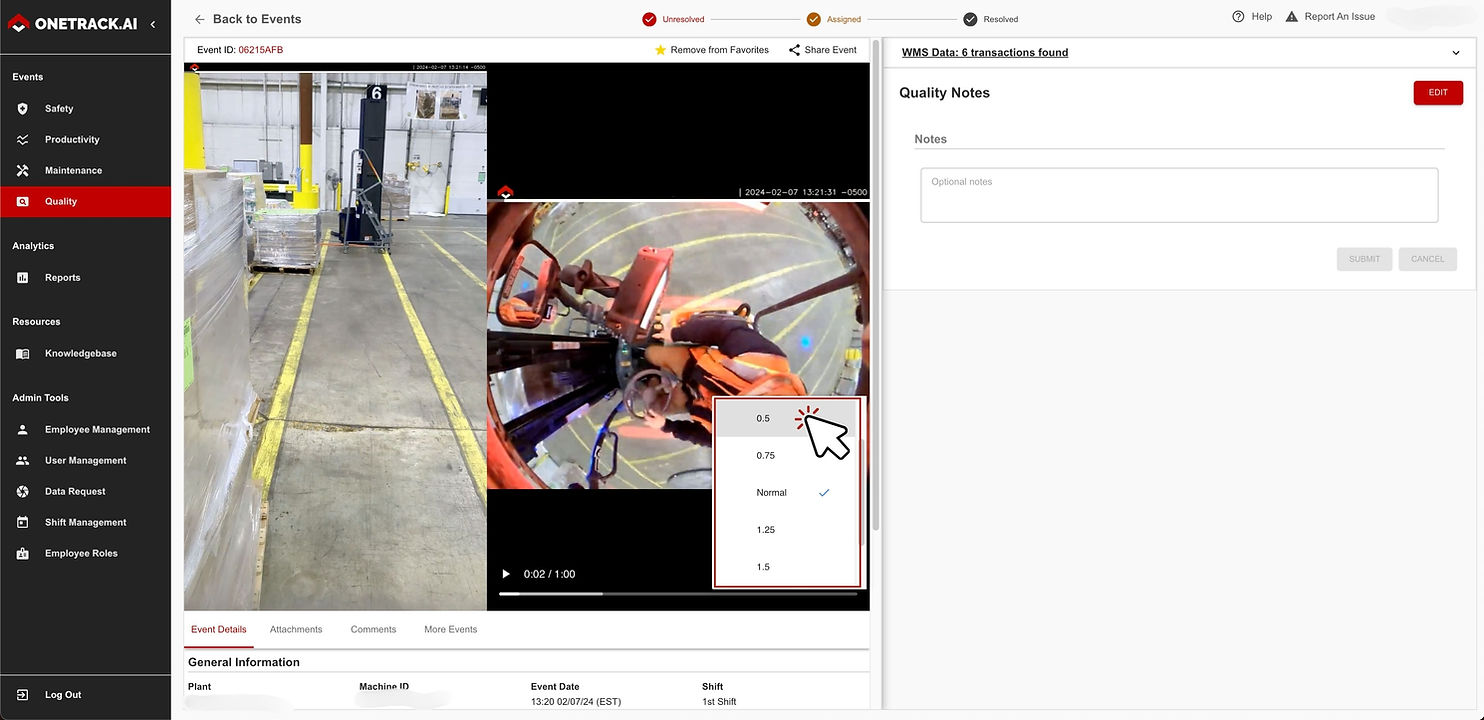
Pro tip: Slow down the playback speed to really drill into the details.Â
‍
After reviewing, you can add comments, review the WMS synchronized data below, and even share directly with your customer or end location for closed loop transparency.
Step 3: Perform a root cause analysis (RCA) for your network
Every world-class operation has one thing in common: the push to be better than they were yesterday. Even if you don’t get any OS&D complaints during a certain period, spending time reviewing your processes is a good habit to form.Â
We recommend at least quarterly to start, but ideally monthly — pick a random sample of events to break down and look for areas of improvement.Â
 A few items to look for:
- Are there specific operators who are involved in the most OS&D claims?Â
- Are operators maneuvering over dock plates safely?Â
- Is the staging area optimized to easily find and load the pallet you need?Â
- Are all operators putting kick-stops and crossbars in place?Â
Over time you’ll be amazed at how much crisper your loading process will become just by spending an hour each month reviewing events, scrutinizing the process, and holding operators accountable.
Want to put this playbook to work for yourself?
Using this playbook is going to help you stay one step ahead of those pesky OS&D issues, maintain trust with your customers (looking at you 3PLs), and ensure goods are going out on time, in top condition.Â
 You now have the ability to:
- Quickly resolve OS&D issues with video evidence
- Continuously improve your loading processesÂ
- Proactively build trust with customers that you’re putting the safety of their product as a top priorityÂ
​Want to put this kind of data to work in your warehouses?
 OneTrack customers, good news! You already have this at your fingertips. Reach out to your implementation manager or support team with any questions.Â
If you aren’t a OneTrack customer, book a custom demo here. We’ll connect to better understand your operations and show you what a partnership could look like.